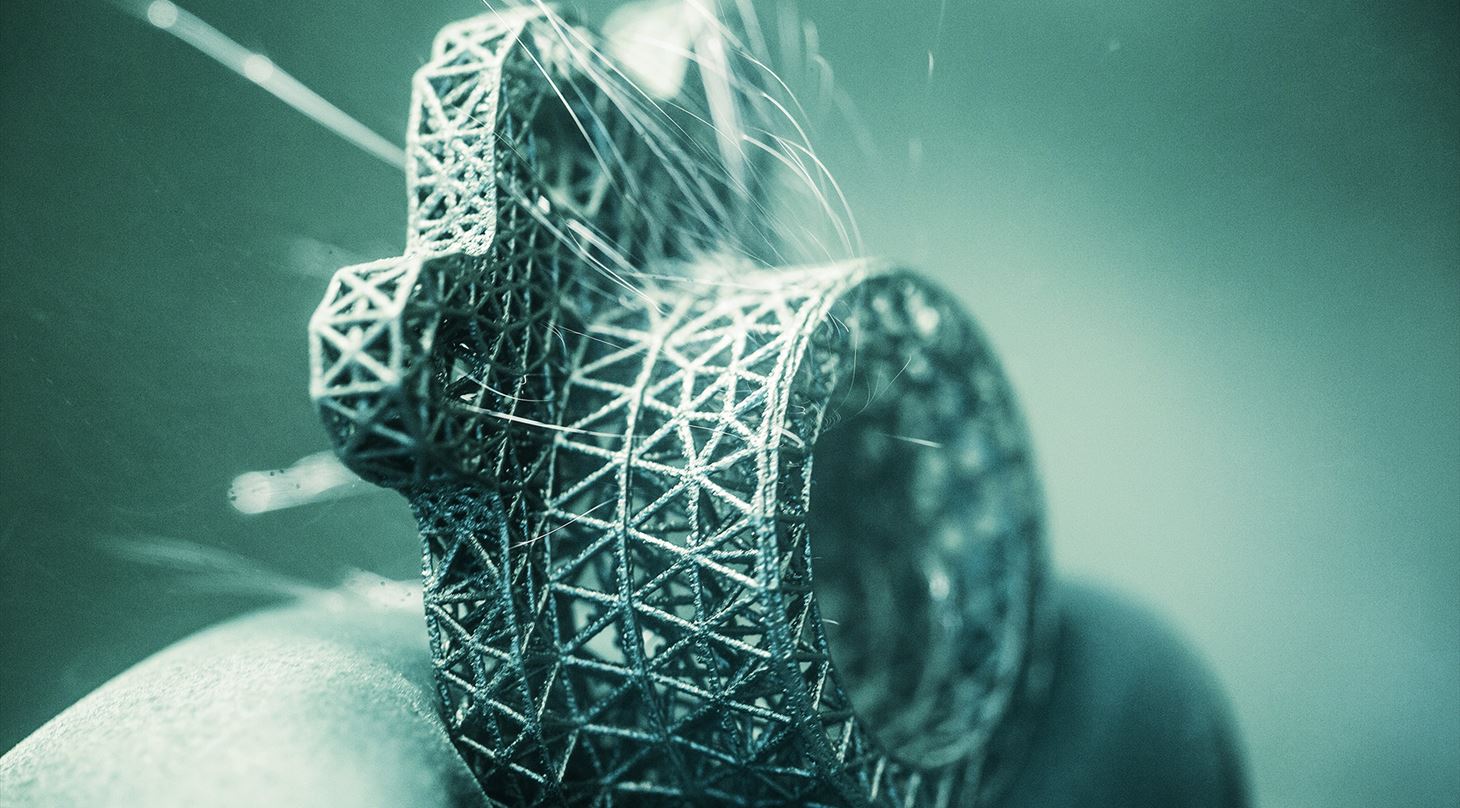
Additive manufacturing creates added value at Danfoss
Danfoss is a global player in technology development, and back in 2016 the company started a digitization journey. Additive manufacturing - or 3D printing – is a key building block in that journey thus creating a need for external production facilities as well as additional knowledge and training in additive manufacturing. Danfoss gets all that in the AM-LINE 4.0 project.
Danfoss develops technologies that enable the world to get more out of less, and the production of mechanical components plays a central role in that business. For a number of these components, additive manufacturing can supplement - and in some cases replace - more well-established manufacturing technologies. Consequently, Danfoss has made a strategic decision to work with additive manufacturing as part of their digitization strategy, and they have allocated considerable resources to it to ensure their competitiveness in this area.
- For Danfoss, additive manufacturing is an obvious choice for several reasons. Firstly, the freedom of design offers an opportunity to increase the product performance of e.g. heat exchangers, and here Danfoss is in a market where it is all about being competitive when it comes to performance vs. price. Secondly, there are several cases where the components will be produced in smaller batches, and here additive manufacturing makes more sense than producing expensive tools for the components, says Jeppe Skinnerup Byskov, head of additive manufacturing at the Danish Technological Institute
Danfoss has chosen to divide additive manufacturing into three categories: prototypes, fixtures and tooling, and end components. Seen in a shorter historical context of additive manufacturing, the first two categories - prototypes and tooling - are more mature, and Danfoss has invested in 3D printers and other necessary hardware to handle manufacturing of these at the company's factory in Nordborg. In addition, a competence center for additive manufacturing is underway in the US, where the knowledge resources will be gathered while the print tasks are outsourced to subcontractors, and there are plans to establish a similar setup in Asia.
- At Danfoss, we have over a million components, and there are many of those components that are suitable for additive manufacturing - and for capturing the added value that additive manufacturing offers. So, we focus heavily on developing a number of our designs for additive manufacturing, says Werner Stapela, Global Head of Additive Design & Manufacturing at Danfoss.
In the video below, Werner Stapela talks about Danfoss' approach to additive manufacturing
Implementing the additive manufacturing mindset in the organization
Danfoss has had an extremely structured approach to additive manufacturing from the very beginning, and in addition to a global head of Additive Design & Manufacturing, an additive manufacturing responsible has been employed in each of the business divisions, just as ‘champions’ have been appointed in the individual groups of the company, who are the go-to persons for additive manufacturing. Furthermore, desktop FDM printers have been installed in the departments to implement the technology in the company as well as in the mindset of the employees. That way, people can experiment with the technology and carry out small tasks, and there have also been internal competitions to encourage people to use the printers.
It has been extremely important for Danfoss to get started with the very concept of additive manufacturing, i.e. teaching people how to design for additive manufacturing and considering the technology as part of the business – it’s not so much about the specific technologies and materials yet. Even though Danfoss has purchased the 3D printers that they specifically needed, the primary focus has been to get employees thinking about additive manufacturing and getting them upskilled in this field – both through internal courses and in collaboration with external partners.
External partners for metal 3D printing
For the production of end components, Danfoss expect most of the components to be in metal, so right the focus is on training and educating engineers and designers, enabling them to develop and design the products for the additive manufacturing production processes in metal. Danfoss does not have immediate plans to handle this production themselves, as it requires specialized knowledge and considerable investments in machinery. Instead, Danfoss will utilize existing competencies in the market and use business partners for the actual production of 3D-printed end components. Here, the AM-LINE 4.0 project, which is funded by the project partners together with the Danish Innovation Fund, plays an important role in Danfoss' strategy - both in terms of education and production.
In this context, the Danish Technological Institute is a key partner for Danfoss in Denmark, since the Institute - which is also the project manager of AM-LINE 4.0 - has Denmark's only Center for Industrial 3D printing in metal. Consequently, Danfoss will collaborate with the Danish Technological Institute to identify relevant cases, discuss design, make prototypes in metal and build up competencies. At some point in the future, Danfoss will then assess whether they should invest in metal 3D printers and handle manufacturing themselves or continue with external partners - and it is far from certain that it makes sense to have machinery and manufacturing inhouse.
But right now, Danfoss is working closely with the Danish Technological Institute through AM-LINE 4.0, and the focus is on how Danfoss can select the relevant items for additive manufacturing, how the business case is set up, and how the items are optimized so Danfoss gets the best value for money - and the most value into the products. For some of the items, the Danish Technological Institute will 3D print prototypes and pilot production, after which there is a request for tenders for the production to ensure the best possible production economy. As a successful global player, Danfoss must focus on costs, and this guides their entire production - so when choosing additive manufacturing and the specific metal items to print, it is because it makes sense from a business perspective.
Assisting a broader uptake of additive manufacturing in Danish industry
Danfoss is a shining example of how to have a targeted approach to working with additive manufacturing work purposefully and utilizing the technological possibilities, and as a partner in the AM-LINE 4.0 project, Danfoss also shows the way for other companies - large and small - who would like to work with additive manufacturing now and in the future.
In AM-LINE 4.0, Center for Industrial 3D printing at the Danish Technological Institute offers a complete production facility, where companies can develop and print products that they can subsequently implement directly in their own production lines. AM-LINE also offers courses and training of companies in the additive manufacturing technology, as well as advice on future investments in additive manufacturing.
- For companies that are new to additive manufacturing, we are able to offer several customized upskilling courses - from shorter inspirational workshops to longer courses with the individual companies. For those companies that are well advanced in the use of additive manufacturing, we can offer guidance on e.g. purchasing 3D printers or choosing subcontractors to scale up production, says Jeppe Skinnerup Byskov.
AM-LINE 4.0 is supported by the Danish innovation Fund