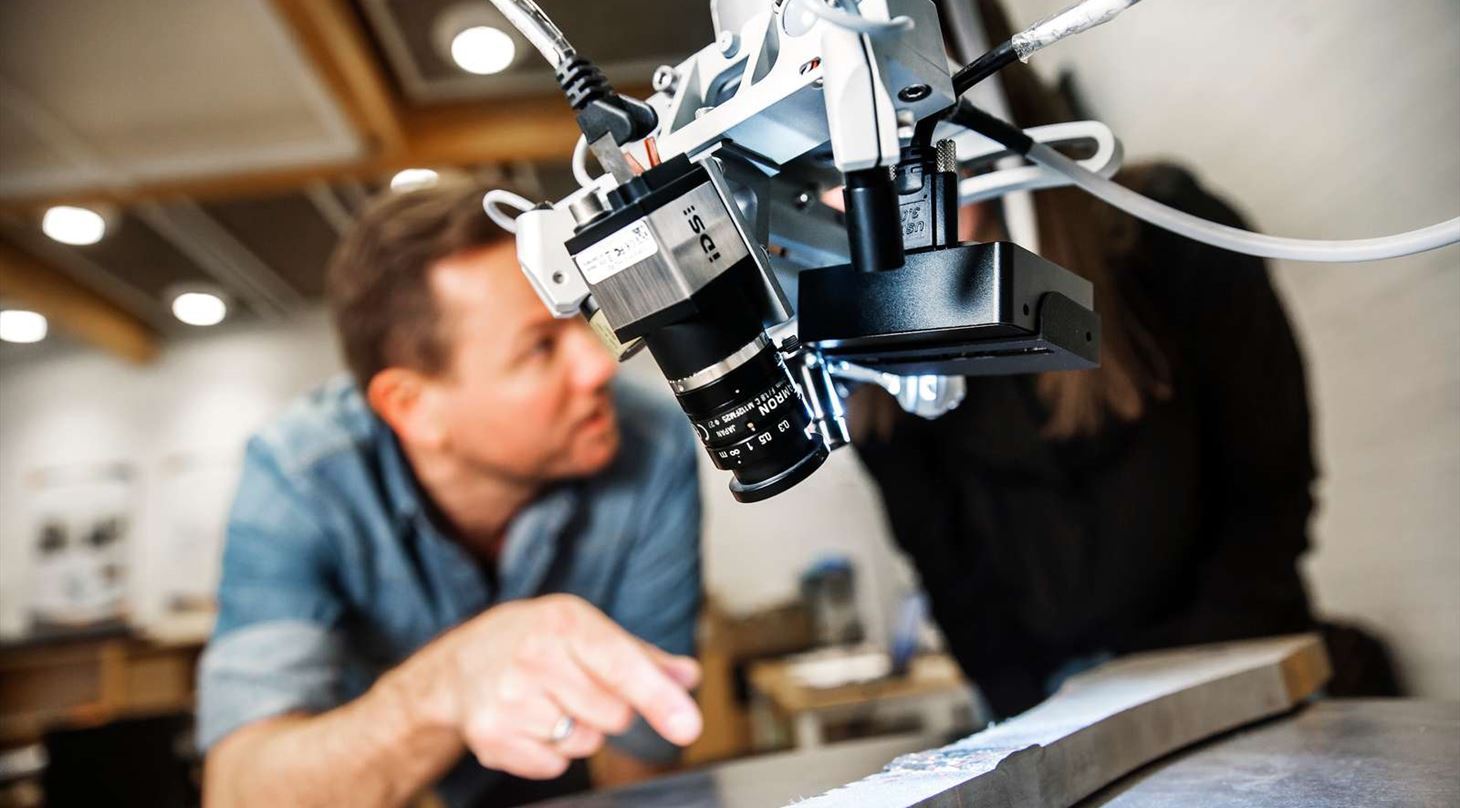
Standardized non-destructive residual stress measurements - in bulk with high resolution
Get control over residual stresses
In any solid metallic component, residual stresses will be present, as they inevitably arise and develop through production processes and during operation. These stresses significantly impact the material's performance and resistance, particularly against cyclic loading. Uncontrolled residual stresses can, therefore, cause premature failure of the component in the form of fractures, fatigue failures, or stress corrosion cracking.
By understanding and controlling the stresses, it is possible to:
- Reduce maintenance costs
The durability and lifespan of a component can be increased by controlling the stress levels in the components and ensuring the absence of uncontrolled stresses, thereby reducing the need for service. This is included in several standards (e.g., DNV-RP-C203: Fatigue Design of Offshore Steel Structures and EUROCODE 3: Design of Steel Structures (EN-1993)). - Reduce component costs
This can be achieved through design optimization. By documenting that the actual stress levels are lower than the typically assumed worst-case scenario values, wall thicknesses and safety factors can be reduced, thereby reducing material consumption. - Reduce the number of warranty claims
- By documenting the actual stress values, the risk of fractures and other failures can be reduced, thereby increasing reliability and operational safety.
- By ensuring production stability, as the presence of residual stresses can cause deformations during the processing of the material, so tolerances cannot be met.
Residual stresses with high resolution at depths of several centimeters
By using the powerful X-ray radiation generated by synchrotrons, residual stresses can be measured at depths of several centimeters (approximately 2 cm in steel and 8 cm in aluminum) with high resolution down to 0.1 mm. This makes it uniquely suited for measuring:
- Residual stresses close to surfaces, e.g., to measure stresses induced by (or in) a coating.
- To verify the effect of surface treatments such as sandblasting, peening, or thermochemical treatment.
- Stress levels in and around critical hotspots at high-stress concentrations.
Standardized measurements pave the way for reliable industrial services
The technique has been known for several decades and is therefore well-established. However, until recently, it has been used almost exclusively in academia. With the development of the new technical specification, DS/CEN/TS 18094:2024, "Non-destructive Testing – Test Method for Determination of Residual Stresses by Synchrotron X-ray Diffraction," software for data analysis, as well as round robin studies (all developed through the EU Horizon project EASI-STRESS), it is now possible to ensure efficient, reproducible, and traceable measurements. This eases access to the measurement service for industrial use.