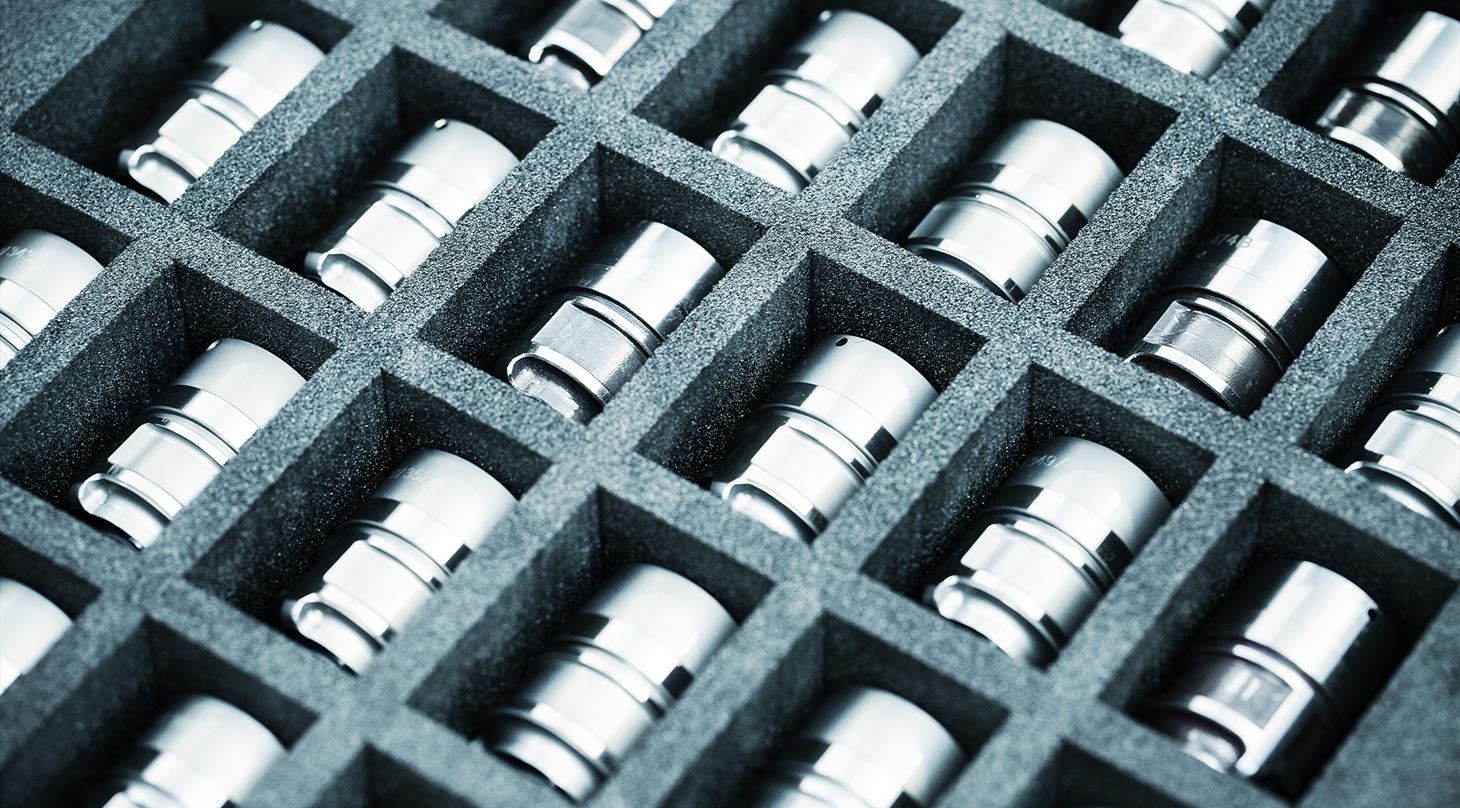
PVD coatings - and other surface treatments
At the Tribology Center, we manufacture a wide variety of PVD coatings for different challenges:
- Extending life span, wear protection, reducing friction, providing corrosion protection, and dry lubrication for production tools, machine parts, and components.
- Release coatings and wear protection for injection molding tools.
- Decorative surfaces with additional special functionalities.
- Surfaces with electrically insulating/conducting, ion-selective, superconducting, catalytically active, or specific optical properties.
We offer a wide range of PVD coatings and can tailor a special PVD coating to your needs. Our standard coatings are typically available with less than one week’s delivery time.
Standard coatings | Other coatings | Special coatings |
CrN-SD, CrN-HP, CrN-SS | TiBto-HP (TiB2) | Oxides |
DLC-TR, DLC-Si* | TiCN-22 | YSZ (Yttria-stabilized ZrO2) |
Versal-HP (TiAlSiN) | AlCrN | Al2O3, |
TiAlN-nano | CGO (CeGdO) | TiO2 |
TiN | ZrN | Metals |
IBAD-DLC* | Ag,Nb, Mo, Cr, W, Hf, Ti, Zr, and more |
*DLC: Diamond-Like Carbon
Many of our PVD coatings are available in “HiPIMS” variants, with a unique PVD technology that creates a highly ionized plasma during the coating process, resulting in smoother, denser, and harder coatings.
We also offer other surface treatments: ion implantation, plasma nitriding, and IBAD (Ion Beam Assisted Deposition).
READ MORE ABOUT SURFACE TECHNOLOGIES
Overview of our tribological surface treatments
HiPIMS PVD coatings
The Tribology Center has developed three new PVD coatings based on the latest HiPIMS technology (HP):
Versal-HP - for particularly demanding machining
A new wear-resistant coating based on the latest HiPIMS technology, particularly suitable for extremely difficult machining tasks. The coating has also demonstrated outstanding lifespan with 40% higher cutting speed. Versal-HP further offers excellent properties for stamping and forming, for example, stainless steel.
CrN-HP - when something extra is needed
A new and improved type of chromium nitride coating that is harder, smoother, and denser. In addition, the coating is extremely ductile despite its high hardness. CrN-HP can therefore increase the lifespan of a wide range of tools, wear parts, and machine components. It is also available in a special Super-Slip (SS) version (CrN-HPSS) for difficult-to-release plastic materials.
TiBto-HP - something special for aluminium and titanium
A brand new coating consisting of the ceramic material titanium diboride, TiB₂. With a hardness of 3800 HV, it is the Tribology Center's hardest coating to date. Suitable for knives as well as punching, forming, and extrusion tools that process cast or rolled aluminum and other adhesive materials.
PVD coatings
CrN – a flexible solution for many purposes
Chromium nitride (CrN) offers a range of beneficial properties, making the coating highly suitable for wear parts, forming tools for both plastics and metals, and a variety of machine components. This coating works well with soft base materials and in thick layers, up to 40 micrometers.
DLC – for dry lubrication of moving parts
Diamond Like Carbon (DLC) is a coating that combines the lubricating properties of graphite with the high hardness of diamond. DLC is suitable for moving parts made of, for example, stainless steel to prevent galling, as well as for tool parts where lubrication is undesirable.
TiAlN – For stamping, forming, and machining
The entire TiAlN group of PVD coatings is characterized by very high hardness and high temperature stability. This makes TiAlN coatings highly wear-resistant, and they have many applications.
TiN – for cutting and shaping of metals
Titanium nitride, TiN, is a classic tribological coating with its characteristic gold color. It is used, for example, for cutting and forming tools to increase wear resistance and prevent adhesion of soft metals such as zinc and brass.
CGO/GDC - Cerium-gadolinium oxide
Cerium-gadolinium oxide coating (Gd₂O₃-doped CeO₂) is an electrically insulating ceramic coating with high oxygen-ion conductivity. It forms a dense and effective barrier in, for example, SOFC and SOEC applications, where it prevents harmful reactions between the cathode’s strontium and the electrolyte’s zirconium, ensuring optimal cell performance and long service life.
TiO2
Titanium dioxide can be used to create catalytic self-cleaning surfaces and is also used to provide special optical properties because TiO₂ has a high refractive index.
Al2O3 (alumina)
Aluminum oxide (alumina) coatings are electrically insulating and can be highly wear-resistant. The coating is used, for example, as an electrical insulator in sliding applications, for sealing surfaces, valve seats, and wherever non-stick, hydrophobic properties are desired for liquids and molten metals. Al₂O₃ can be applied with or without a bonding layer and can be adapted for both conductive and insulating substrates.
YSZ - Yttria-stabilized ZrO₂
YSZ-8 (yttria-stabilized zirconia) is a dense and durable ceramic coating used as an electrolyte in fuel cells. Ultratthin, dense, and crack-free YSZ films, produced using PVD technology, ensure efficient ion conduction, low resistance, and high durability - enabling highly reliable, efficient, and cost-effective solutions even at lower temperatures.
Pure metal coatings
In addition to the ceramic PVD coatings mentioned above, we can also provide coatings consisting of pure metals. These metal coatings include, among others: Silver (Ag), Niobium (Nb), Molybdenum (Mo), Chromium (Cr), Tungsten (W), Hafnium (Hf), Titanium (Ti), Zirconium (Zr), and more.
Ion implantation – the invisible strength
Ion implantation can be used to shoot high-energy ions into a surface. This is used, for example, to create our unique SuperSlip coating (CrN-SS) for injection molding tools. The method is also used to produce our self-lubricating IBAD-DLC for, e.g., forming tools for sheet metal packaging.
Plasma nitriding – the modern nitriding process Plasma nitriding is used for nitriding and nitrocarburizing steel at lower temperatures than traditional processes. The result is hard and wear-resistant surfaces with good sliding properties. With plasma nitriding, there is minimal risk of distortion and deformation of the component. Plasma nitriding can be performed so that only a selected part of the surface is treated.