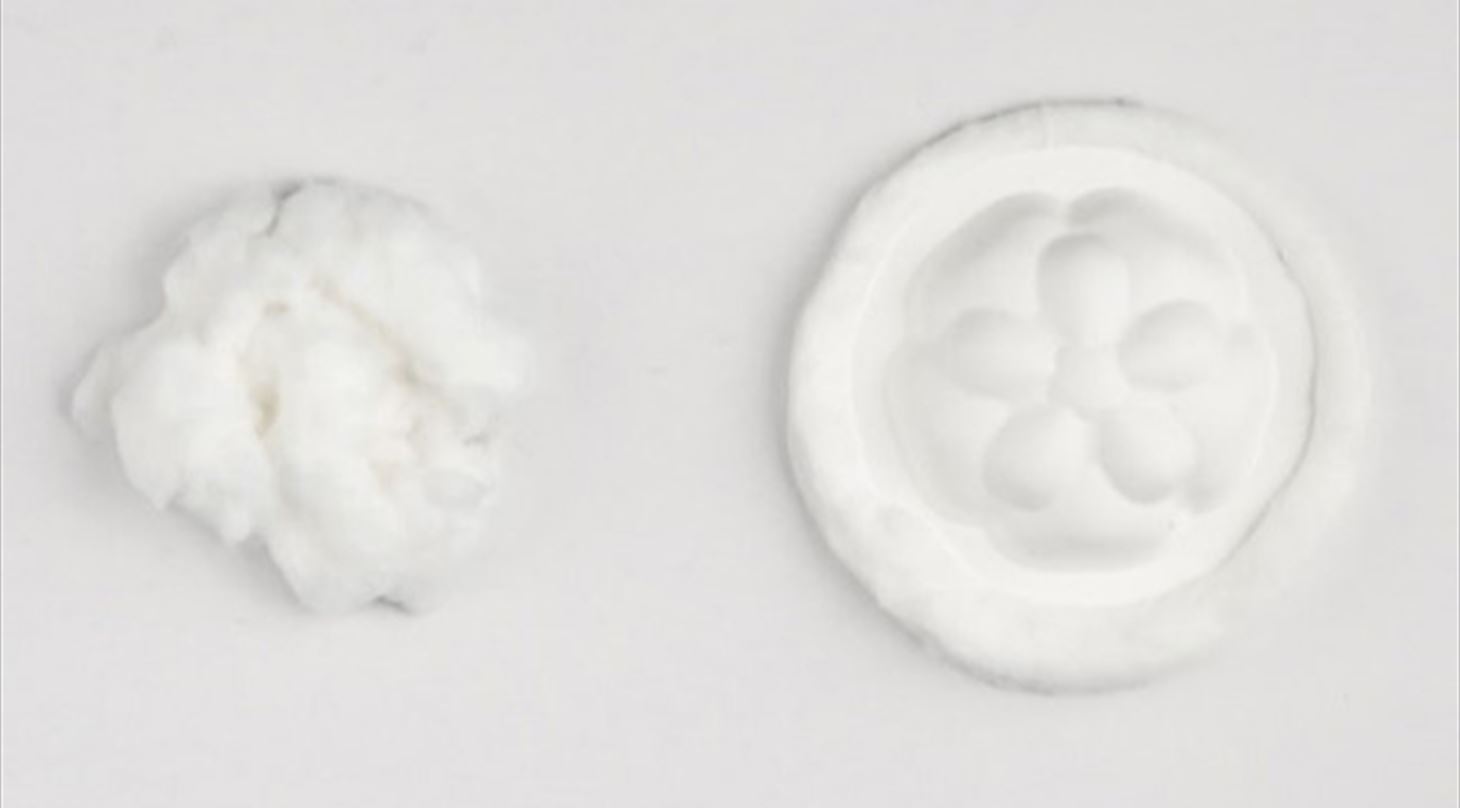
Optimizing novel cellulose dry-forming method
The Swedish start-up Yangi AB teamed up with the Danish Technology Institute (DTI) and DESY to use X-ray scattering measurements at PETRA III, to understand the effects of manufacturing compression conditions to the mechanical properties of more sustainable packaging solutions.
Challenge
Yangi AB supports brands and converters in achieving their sustainability targets by helping them transform their packaging portfolio into new, alternative, renewable and sustainable packaging solutions that offer competitive production costs, fully renewable raw materials, and resource-efficient production. Yangi AB has developed a ground-breaking, dry-forming technology to create 3D-formed, cellulose-based packaging that doesn’t need any process water, by using a combination of air-laid formation and fast pressing of the cellulose fibers. This technology promises lower energy consumption and lower CO2 emissions. Cellulose materials fulfill the key requirements of recyclability, rigidity, sustainability and 3D formation, making them a viable alternative to replace rigid plastic.
I had a great experience collaborating with DTI. It was clear from the start that they were knowledgeable, expertly guiding us through the design process of our experiment, delivering beneficial and timely results. Their method gave us valuable insight into developing our own process within Yangi
- Polina Naidjonoka, Material Scientist, Yangi
Method
High quality scattering data (Figure 1) were obtained through the collaboration between the Danish Technological Institute (DTI) and the German national accelerator DESY. The measurements of this project have been carried out at PETRA III’s Micro- and Nanofocus X-ray Scattering Beamline P03 (Figure 2). During this beamtime, the effect of the e.g. temperature and compression pressure on the performance of the final product was tested by characterizing the samples using ultra-small-angle and wide-angle X-ray scattering (USAXS and WAXS) with high flux synchrotron radiation.
Figure 1: USAXS and WAXS data respectively obtained at PETRA III’s P03 beamline
Insights and Analysis
The structure of the cellulose material is important for the final performance of the product. Structural features such as the fibril arrangement and the degree of crystallinity can be probed at a broad range of length scales. WAXS delivers information at the nanometer scale, and USAXS at the micrometer scale. Due to the extremely high brilliance of PETRA III, the necessary photon flux is available to collect high quality data from weak scattering materials like cellulose, which is not possible at a lab-based X-ray source.
Figure 2 - left) Team while measuring at the at the beamline P03, PETRA III; Veronica Lattanzi (BM DTI), Benedikt Sochor (Post Doc, DESY), Hanna Leemreize (Sr Specialist, DTI); right) WAXS detector (top right) and flight tube for the USAXS detector (in the middle), at the beamline P03 at PETRA III.
Benefits
Multiple samples were fully characterized on the nanometer length scale in a short period of a few hours. The service proves the possibility to understand the structure of the fiber material in detail by using advanced characterization at large scale research infrastructures, besides showing the effects of processing parameters on the performance of the final product.
The service opens up a path to understand the microfibrils’ alignment and changes in the crystallinity of the product better, depending on various temperatures and pressures.
This can further lead to the optimization of the compression procedure and selection of the raw material, as well as a better design of a compressed shape.