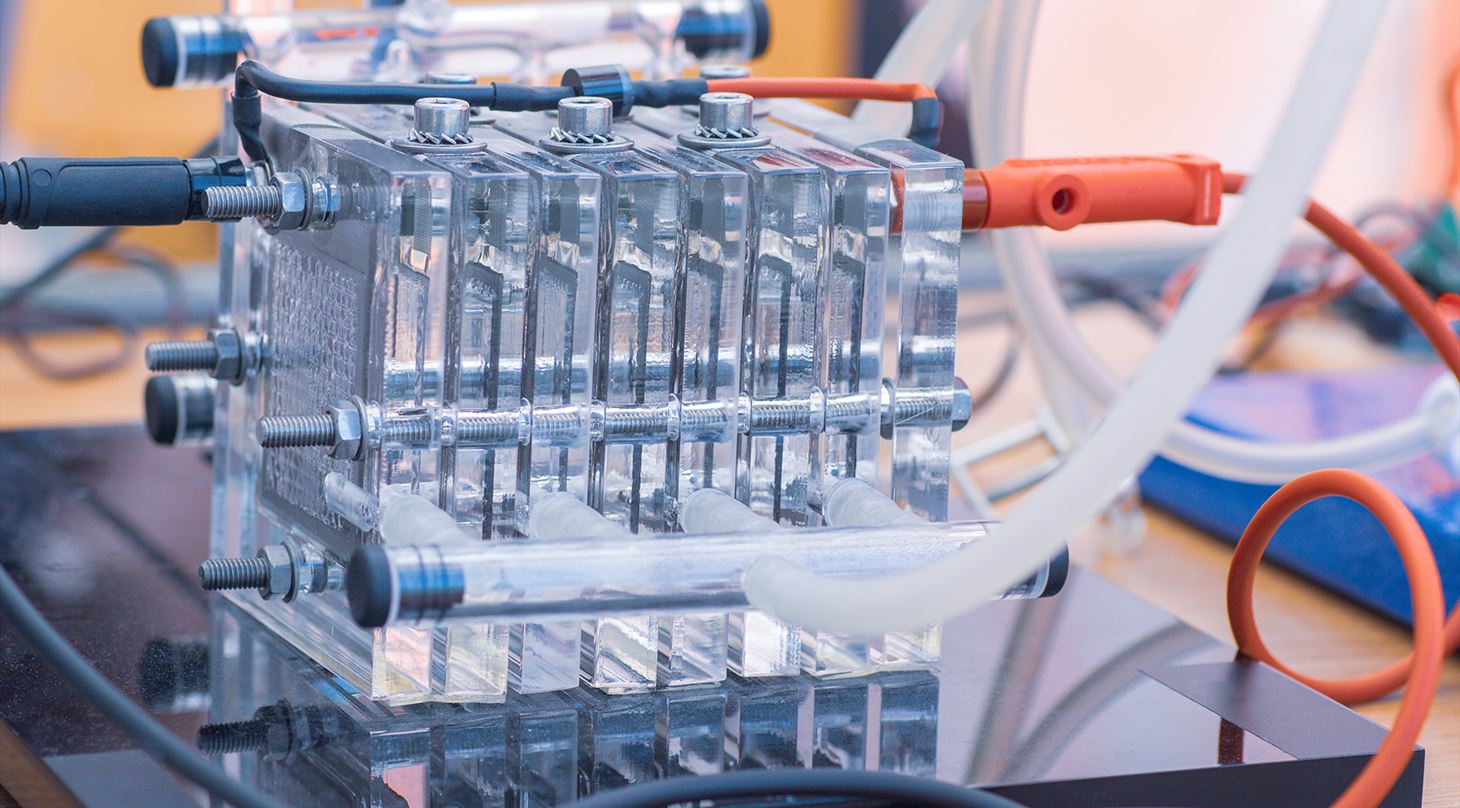
Neutron technology provided insight into electrolysis cells
The Danish company Advanced Surface Plating optimizes electrolysis cells to produce green hydrogen based on alkaline electrolysis. In this context, there was a need for insight into the processes taking place inside the cells, and neutron technology was used with the help of specialists from the Danish Technological Institute in advanced characterization.
Green hydrogen production is an essential technology for the green transition. However, with the solutions available today, it would be expensive and require a large number of raw materials and wind turbines to produce enough green electricity for the hydrogen production, for example, to produce steel with it or fuel for airplanes and container ships. Therefore, we need more energy efficient solutions to produce green hydrogen, and that is precisely what the company Advanced Surface Plating (ASP) is working on: making electrolysis cells for the production of green hydrogen more energy efficient.
ASP has already made significant progress with the optimization, and it has saved a significant amount of the electricity used to produce green hydrogen - enough to save a large number of offshore wind turbine parks worldwide when global container shipping transitions to fuel made with Power-to-X.
Where are the bubbles formed?
However, there is still potential for further optimization, and ASP would like to have better insight into the processes that occur inside a working electrolysis cell. The challenge is that it occurs behind several layers of metal inside some electrodes made of a metal foam. This is where the hydrogen is generated in the form of bubbles, which run through the cell, and it is impossible to see the bubbles in the water inside the cell between all these layers with normal light.
On the other hand, neutrons have a unique ability to see hydrogen-containing materials through other materials such as metal.
With neutrons, it is possible to take pictures and make movies of what is happening inside the working electrolysis cells - and see where the bubbles are formed and how they flow through the cells. In this way, a better understanding of how the process works and how it can be further optimized
- Jonas Okkels Birk, Danish Technological Institute
Building bridges between industry and research
The specialists at the Danish Technological Institute in advanced characterization have extensive knowledge of neutron measurements and collaborate with a number of research facilities worldwide where it is possible to make this type of measurements - therefore, the Danish Technological Institute can bridge the gap between industry and research.
In this case, ASP and the Danish Technological Institute collaborated on a pilot project through Energy Cluster Denmark, where measurements were made on a couple of the electrolysis cells under different conditions. Specifically, the Danish Technological Institute and ASP took the electrolysis cells to the measurement facility, where they were responsible for making the measurements. This took place at the Paul Scherrer Institute in Switzerland - an advanced research facility in the billion-dollar class, which does not have a corresponding facility in Denmark.
In the process, the Danish Technological Institute has been able to contribute knowledge about where to have these measurements made, how to plan the measurements in practice, and how to measure the right things - so they helped to find a facility and a solution that matched the concrete industrial challenge. In addition, the Danish Technological Institute took part of the measurement execution and were available with input for the data analysis.
The pilot project showed great potential for neutron measurements, and based on the initial results, ASP has already gained insight into where the hydrogen bubbles are created in the cells and whether they flow as planned through the cell or are trapped in the electrode foams. This knowledge has, among other things, already been used to optimize the design of the electrolysis cells.
Further collaboration Grand Solution project
The results were so promising, that ASP, the Danish Technological Institute, HydrogenPro and Aarhus University have applied for and received funding for a Grand Solution project through the Innovation Fund Denmark.
In the Grand Solution project, new measurements will be made, to investigate the effects of electrode thickness, pore size and special treatments developed by ASP.
In this context, Aarhus University will create some large computer models to simulate and optimize the processes inside the electrolysis cell. The physical neutron measurements will be used to verify the computer models and provide input to them. So far, they have primarily used measurements of how much hydrogen is produced at different current levels as input parameters to validate the computer models that have been made
It is a bit like trying to simulate a car engine by looking at how fast the car is running and knowing how much pressure is applied to the accelerator - but not really knowing what is happening inside the engine. With neutron measurements, it is actually possible to look under the hood and see what is happening inside the engine, to stick with the comparison.
The neutron measurements make it possible to create even better computer models, which in turn can make it possible to achieve even more energy efficient electrolysis cells.