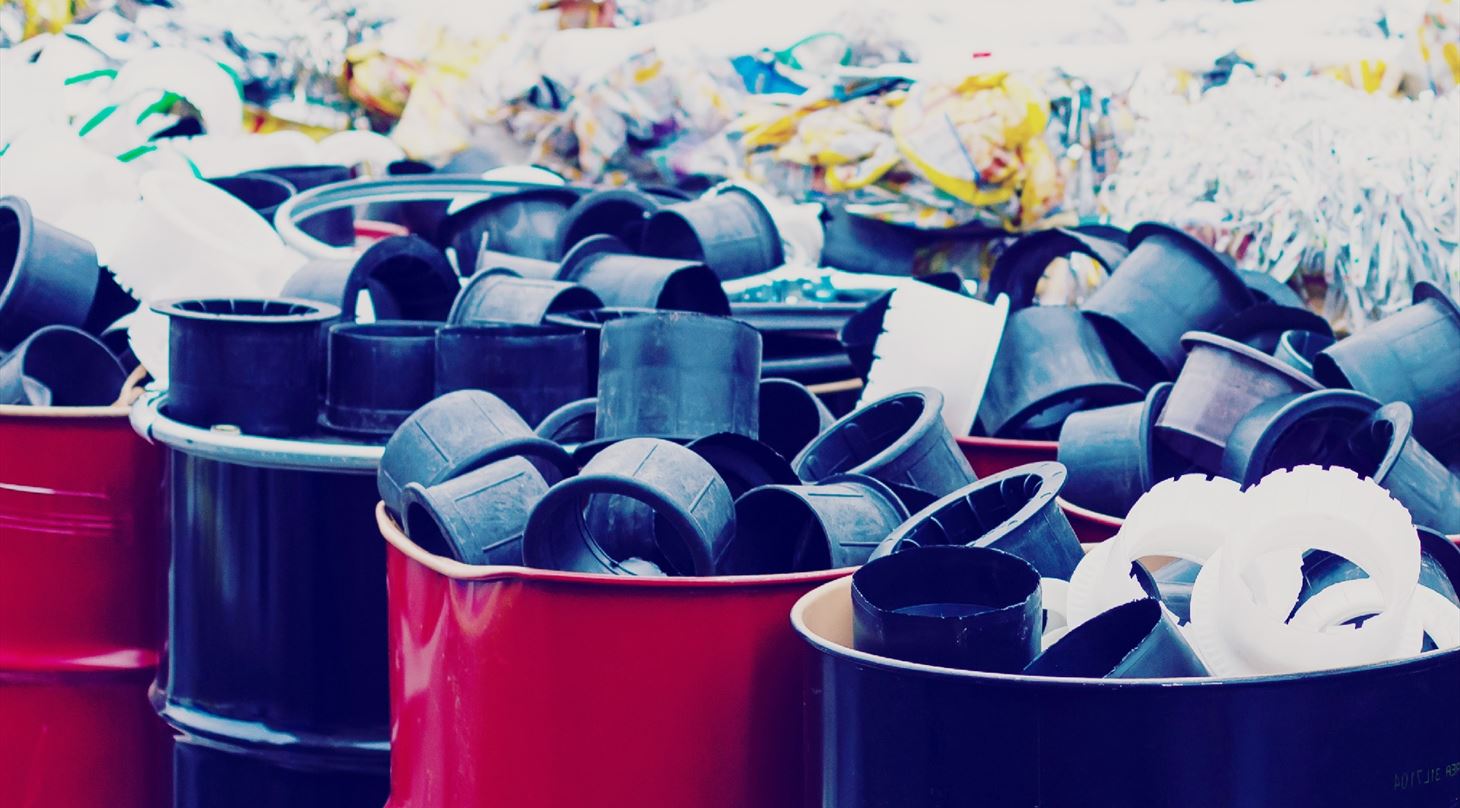
Key industrial companies join forces against plastic waste
The ambition of the new partnership is to increase recycling of industrial plastics by at least 20 percent before 2025 and to create a new platform for recycling of plastics in Danish companies.
Today, many industrial products made of plastic are incinerated or landfilled after use because they either are not designed for recycling or because the available recycling technologies cannot handle the products. Several of the largest Danish companies have joined forces to make a change and aim at increasing the recycling rate by at least 20 percent before 2025.
The project partners, i.a., comprise Coloplast, Novo Nordisk, Danfoss, Topsoe, BASF, Grundfos, and COOP. Danish Technological Institute has united the companies in a project called Circular Industrial Plastics (CIP) that has a total budget of 41m DKK, of which 18m DKK were granted by the Danish Eco-Innovation Program (MUDP) under the Danish Ministry of Environment.
– We produce too much plastic that is only used once and then it is thrown away. Therefore, it is superb that leading Danish key industrial players are joining forces to increase recycling of industrial plastics. In Denmark we are good at finding solutions together, which this project brilliantly illustrates. Society is created to consume enormous amounts of resources and could be compared with a super-jumbo that has to change its course. This project will definitely contribute to a step in the right direction, says Ms. Lea Wermelin, Danish Minister of Environment.
A new circular puzzle
Key players do not usually join forces:
– It is unique that so many large and different companies co-operate across sectors and value chains. It is also an advantage as merely the size of the companies makes it easier to quickly upscale and implement the solutions. Together we can now discuss how we can create new circular material flows that work technically, financially, and environmentally. A new circular puzzle will be solved, says Sune Dowler Nygaard, Executive Vice President, Danish Technological Institute.
Rethinking technologies and products
The circular puzzle will for instance be resolved by matching product materials with available recycling technologies. The project will investigate how plastics in products designed with focus on functionality and longevity – but not necessarily on recycling – can be used again for producing similar or other products of same quality. Alternatively, it may be necessary to decompose the material chemically and convert it into raw material for new plastic production. The project will also investigate how future products should be designed in preparation for recycling at end-of-life.
– When designing products, it is important to bear the products’ end-of-life in mind, so circularity is ensured in the future. That is why joining forces on recycling technologies is essential to achieve success’, says Head of ESG at Danfoss Climate Solutions, Ms. Nanna Aage Lundsgaard.
– The project will demonstrate that products as well as technologies can be adapted for increasing circularity – not only within one company but across companies. As we operate within several industries in the project it will be possible to pool plastic streams and obtain synergy effects that benefit the economy and the environmental gain of the solutions, says Project Manager, Dr. Søren Haack, Danish Technological Institute.
New solutions can provide impetus to legislation
Among the participating companies, the medico companies Novo Nordisk and Coloplast experience specific challenges. Plastics from used medical equipment are subject to strict legislation, resulting in the majority of medical plastic being incinerated or landfilled after use. However, if new recycling solutions also can ensure the pureness of the reprocessed plastic, it might provide an impetus for change in legislation and ensure circularity within the trade.
– At Novo Nordisk we are creating a Recycling Scheme (PenCycle) for our patients so they can return used plastic insulin pens. The pens are categorized as hazardous waste and previously they were incinerated. Much legislation was made before circular economy became essential. Therefore, it is vital to have a constructive dialogue with the authorities, so legislation supports circularity and recycling of plastic, says Dorethe Nielsen, VP Corporate Environmental Strategy at Novo Nordisk.
Cannot be solved single-handedly
The first step in the CIP project will be to map and investigate the plastic materials that are currently used in the companies and then create an infrastructure for further treatment and recycling.
– Industrial plastic is a very important material group, and it is possible to create functional design from the material. However, Grundfos assumes responsibility for the full value chain and for the end-of-life product. It is a very complex task to match materials and end-of-life circular technologies. Grundfos cannot accomplish that on its own. So besides inspiring other companies, Grundfos also wants to strengthen its “toolbox” regarding legacy products and the design of new products, says Preben Jakobsen, Chief Engineer, Grundfos.
Easy access to circular plastics
The project will implement full-scale recycling solutions for selected products within the categories of medical, technical, and consumer plastics, and furthermore demonstrate how new recycling technologies can interact in a circular economy.
Furthermore, the ambition is that the CIP project will give Danish companies access to new knowledge and technologies for establishing circular flows within plastics.
– The CIP project lays the foundation for a platform that matches materials and recovery technologies. This will give Danish companies easy access to co-operation and knowledge about specific solutions that can be implemented immediately – but also access to knowledge about how to innovate in the future. In short, the project will be a catalyst for the transition from linear to circular production and the use of plastics, says Dr. Lars Haahr Jepsen from Danish Technological Institute.
The project Circular Industrial Plastics (CIP) is supported by the Danish Ministry of Environment and is a so-called flagship project where solutions will be tested and demonstrated in full-scale to inspire Danish trade and industry.
Participants in the CIP project
Plastics consuming industrial companies
- Novo Nordisk A/S
- Danfoss A/S
- Coloplast A/S
- Grundfos A/S
- F&H A/S
- Coop Danmark A/S
Reprocessing, infra structure and recovery
- Trebo ApS
- Zirq Medical A/S
- Makeen Power A/S
- Crossbridge Energy A/S
- Topsoe A/S
- Marius Pedersen A/S
- Geminor ApS
- BASF A/S
Knowledge partners
- Aarhus University
- DTU, Technical University of Denmark
- Danish Technological Institute (project manager)
Contact
Søren Haack, Danish Technological Institute
Project Manager, PhD
Cell +45 72 20 23 38
Mail: sorh@teknologisk.dk
Lars Haahr Jepsen, Danish Technological Institute
Team Manager, PhD
Cell +45 72 20 19 27
Mail: laje@teknologisk.dk
Website