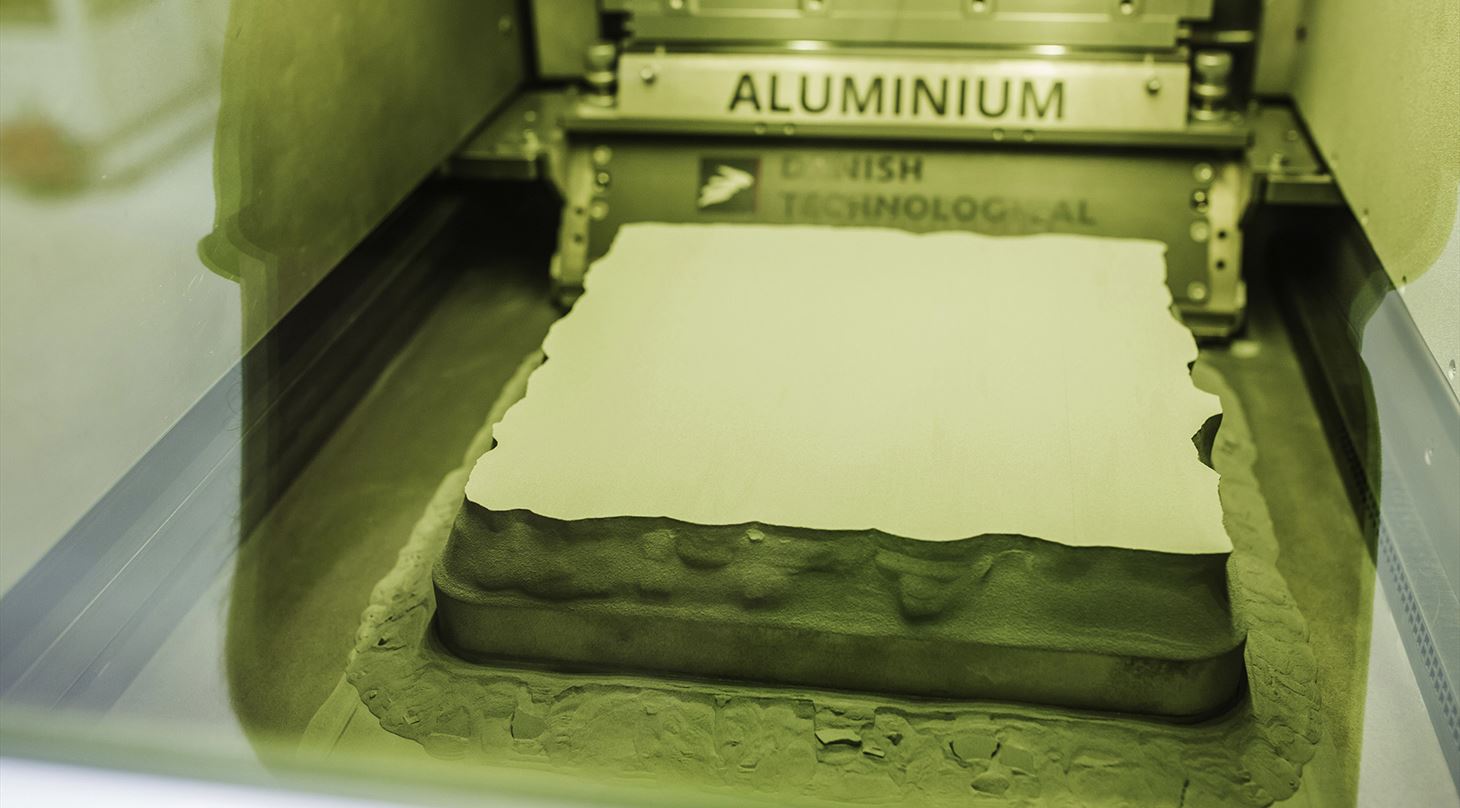
Introduction to 3D printing - AM technologies
Select Page
What is Additive Manufacturing?
The term Additive Manufacturing (AM) - also called 3D-print - covers many different technologies that can be used with a wide range of different materials such as metal, plastic, ceramics and wax to produce (i.e. print) ready-made items directly from a digital 3D CAD file.
Digital 3D CAD file (left) and photo of printed item (right)
Depending on the application, the AM designation is typically divided into Rapid Prototyping (RP) and Rapid Manufacturing (RM). Rapid because the number of production steps is low compared to most other forms of production (ideally only one) and because the production is not dependent on the manufacturing of special tools or molds first. Consequently, the technology is an inexpensive alternative to conventional manufacturing technologies for small batch sizes.
The graphs show typical unit price trends as a function of the serial size for Additive Manufacturing and traditional production respectively.
AM technologies
In the most common forms of Additive Manufacturing, the items are built up layer by layer in the desired material in the AM machine (i.e. the 3D printer) - e.g. by melting, welding or gluing thin layers of powder together, hardening liquid using UV light, or melting thin plastic wires together. The most common AM technologies are described below.
- Stereolithography (SLA)
SLA uses a UV light in the form of a single-point laser source to cure (solidify) liquid resin in a vat layer-by-layer.
SLA can produce parts with very high dimensional accuracy, intricate details and a very smooth surface finish ideal that are ideal for visual prototypes. A large range of speciality materials, such as clear, flexible, castable and biocompatible resins, or materials tailored for specific industrial applications, are also available. - Selective Laser Sintering (SLS)
The SLS process begins with heating up a bin of polymer powder to a temperature just below the melting point of the material. A recoating blade or roller then deposits a very thin layer of powder - typically 0.1 mm thick - onto the build platform. A CO2 laser scans the surface of the powder bed and selectively sinters the particles, binding them together. When the entire cross-section is scanned, the building platform moves down one layer and the process repeats. The result is a bin filled with parts surrounded by unsintered powder.
SLS parts have very good, almost-isotropic mechanical properties, so they are ideal for functional parts and prototypes. Since no support structures are required (the unsintered powder acts as support), designs with very complex geometries can be easily manufactured. SLS is also excellent for small-to-medium batch production (up to 100 parts), since the bin can be filled throughout its volume and multiple parts can be printed at a single production run. - Selective laser Melting (SLM)
Selective Laser Melting (SLM) produce parts in a similar way to SLS: a laser source selectively bonds together powder particles layer-by-layer, and SLM achieves a full melt of the powder particles. As opposed to SLS, however, SLM produce parts out of metal.
SLM is ideal for manufacturing metal parts with complex geometries that traditional manufacturing methods cannot produce. SLM parts can be (and should be) topology optimized to maximize their performance while minimizing their weight and amount of material used. SLM parts have excellent physical properties, often surpassing the strength of the rough metal. Many metal alloys that are difficult to process with other technologies, such as metal superalloys, are available in SLM. - Fused deposition modelling (FDM)
In FDM, a spool of filament is loaded into the printer and then fed to the extrusion head, which is equipped with a heated nozzle. Once the nozzle reaches the desired temperature, a motor drives the filament through it, melting it. The printer moves the extrusion head, laying down melted material at precise locations, where it cools and solidifies (like a very precise hot-glue gun). When a layer is finished, the build platform moves down, and the process repeats until the part is complete.
FDM is the most cost-effective way of producing custom thermoplastic parts and prototypes. It also has the shortest lead times - as fast as next-day-delivery - due to the high availability of the technology. A wide range of thermoplastic materials is available for FDM, suitable for both prototyping and some functional applications.
The figure below shows an illustration of the principle behind Selective Laser Sintering (SLS). The principle is the same for Selective Laser Melting (SLM), the only difference being that the energies used are much higher, since the printing is done in metal. The principle of the SLA printer is slightly different, using liquid (photopolymer) instead of powder, but the process is similar to SLS and SLM: A platform is moved downwards in a vessel with photopolymer liquid, and the items are built layer by layer using a UV laser.
Illustration of the principle behind the SLS technique. The plastic items (a) are printed layer by layer on the platform (b), which is slowly moved downwards in 0.12 mm steps as a new layer is built on top of the item. A powder dispenser (c) ensures that a new layer of powder is added each time the platform and item are moved down one step. The building process itself is handled by a laser (d) which scans over the surface by means of a rotatable mirror (e) and sinters the plastic particles together – also with layer underneath - in the desired (two-dimensional) geometry. In addition, to fill the powder dispenser with powder and collect excess powder, the machine is equipped with two powder containers (f) and two collecting containers (g). During the printing process, the items are surrounded by loose powder (h) which, together with the powder in the collection containers, can be recycled. The chamber and powder are heated by infrared lamps and heating elements.
The layered structure of the items in the 3D printer is illustrated in the figure below.
The items are built layer by layer in the printer. The figure shows an item after 10, 30, 50, 70, 90, 110, 130 and 150 layers.
Compared to traditional manufacturing technologies
Additive Manufacturing is a fast, precise and flexible form of production. With AM, you are not bound by the same geometrical limitations as you experience with traditional manufacturing technologies, and you can essentially produce anything that can be drawn in a computer. AM is particularly suited for fast and precise production of prototypes, and for direct serial production of items with high geometric and/or structural complexity, items with special functionalities or properties, individually customized items, products where changes are needed to the design during the process, or if you need quick production of relatively few items.
The process parameters used during the actual construction process can be used to tune the mechanical and physical properties of the finished item. In the SLM machine for instance, you can vary e.g. laser power, laser speed and distance between the laser paths. This allows for the control of the microstructure and material properties of the finished metal item, thereby achieving unique functionalities.
Overview of machines
At the Danish technological Institute, we have a wide variety of Additive Manufacturing technologies, and via our network we have access to even more.