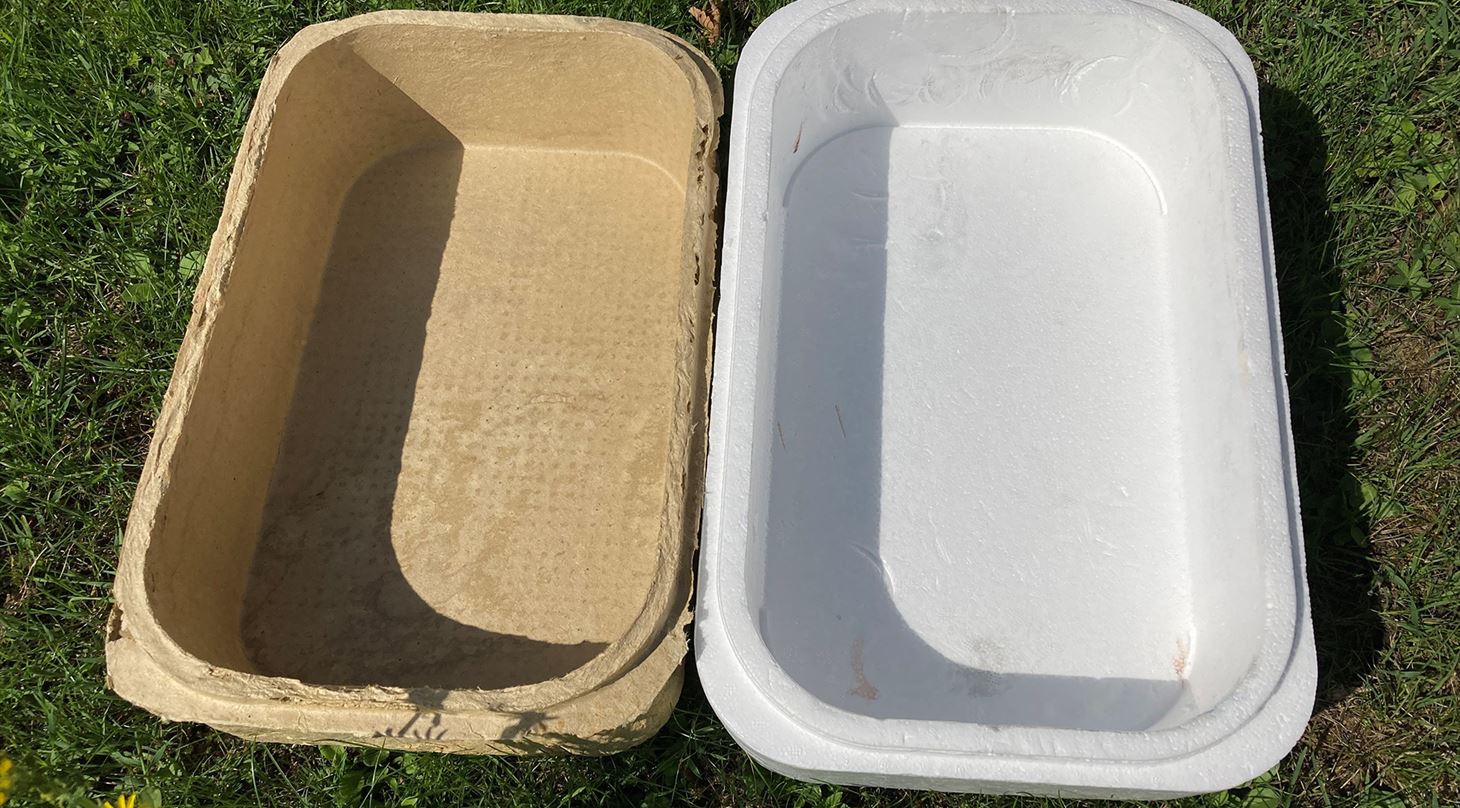
From polystyrene to grass fibre packaging – an innovative journey
The packaging specialists at the Danish Technological Institute have assisted the Icelandic startup Coolity in developing a new type of grass fibre box, initially intended for the transport of fish from Icelandic fish farms. The box is developed as an alternative to the traditional expanded polystyrene boxes currently in use.
It all began with a vision from Anna María Pétursdóttir, CEO of Coolity. She wanted to use locally available materials to develop a packaging alternative to the traditional boxes made from expanded polystyrene (EPS) that are used in e.g. the Icelandic fishing industry.
- Coolity was founded with the desire to transform unused natural materials into valuable and more sustainable products that can reduce dependence on fossil-based materials. Concerned about plastic pollution in the oceans, we explored the potential of using natural materials for new packaging solutions to transport fresh fish, says Anna María Pétursdóttir, CEO of Coolity.
Challenges with EPS
EPS – also known as Styrofoam – is a fossil-based material that is not biodegradable. Moreover, it is a material that easily fragments, thereby contributing to pollution. When an EPS box fragments, small pieces of polystyrene foam can form, which risk ending up in aquatic environments.
Coolity sought to develop packaging that could meet the same needs as EPS in terms of insulation and durability, but which uses alternative materials and production methods to address the challenges associated with EPS.
From wool to grass fibre
Coolity’s original idea was to use wool as an insulating material in a double-sided cardboard box, as Iceland has abundant wool supplies. However, this solution proved impractical due to wool's tendency to absorb moisture. Additionally, there were logistical challenges in assembling the box before use.
In 2022, Coolity reached out to the Danish Technological Institute to find an alternative solution. The institute was able to contribute with expertise in advanced materials and moulding techniques, and instead of wool, the focus shifted to grass fibres. Iceland has vast areas of unused grassland, making the raw material easily accessible. Grass fibres have natural water- and grease-repellent properties due to their high lignin content. This would provide a more environmentally friendly packaging solution that reduces dependency on fossil-based materials – but it would also require significant effort.
- Coolity’s challenge required an entirely new approach to packaging production. Traditional moulding methods were insufficient, as they typically focus on creating thin walls, whereas this box needed greater thickness to achieve the required insulation properties, says Alexander Leo Bardenstein, material specialist and business manager at the Danish Technological Institute.
Danish Technological Institute delivers innovation power
The Danish Technological Institute proposed an innovative moulding process that mimics injection moulding but uses a wet dispersion of cellulose fibres to create a solid yet porous structure. The Institute had prior experience with using grass fibres from an earlier project and was therefore familiar with the properties of the material.
- Grass fibre pulp primarily consists of water – up to 99 % – making it necessary to drain and dry the material carefully to preserve its porous structure and ensure its insulating properties, explains Alexander Leo Bardenstein.
The Danish Technological Institute’s solution was a two-step drying method was required: first, excess water is removed, and then the material is gently dried to maintain its porosity. This process ensures that the box achieves the desired insulating properties.
Utilizing local resources
Throughout the project, the Danish Technological Institute played a central role in transforming an idea into a tangible prototype, enabling Coolity to file a patent application for the innovative technology. The collaboration with Coolity demonstrates how the Institute’s expertise can drive the development of solutions that are more sustainable as well as commercially viable – and it emphasizes the importance of technological innovation in the green transition.
In the long term, this groundbreaking solution has the potential to impact the packaging industry on a global scale. It not only offers a viable alternative to EPS but also utilizes local resources in a more sustainable way while supporting the local economy.
The collaboration not only resulted in a prototype but also provided Coolity with a deeper understanding of how to effectively use local resources, such as grass fibres, in packaging production.
The collaboration with the Danish Technological Institute has been crucial in accelerating our innovation process. With valuable insights, technical expertise, and innovative tools, they have contributed invaluable knowledge that has expanded our perspectives. The joint effort has led to more creative and efficient solutions in the development of Coolity’s cooling boxes and significantly elevated our results
- Anna María Pétursdóttir, Coolity
With the prototype, Coolity has subsequently been able to apply for – and receive funding for – a development project to further refine the solution, with the Danish Technological Institute continuing as a subcontractor.