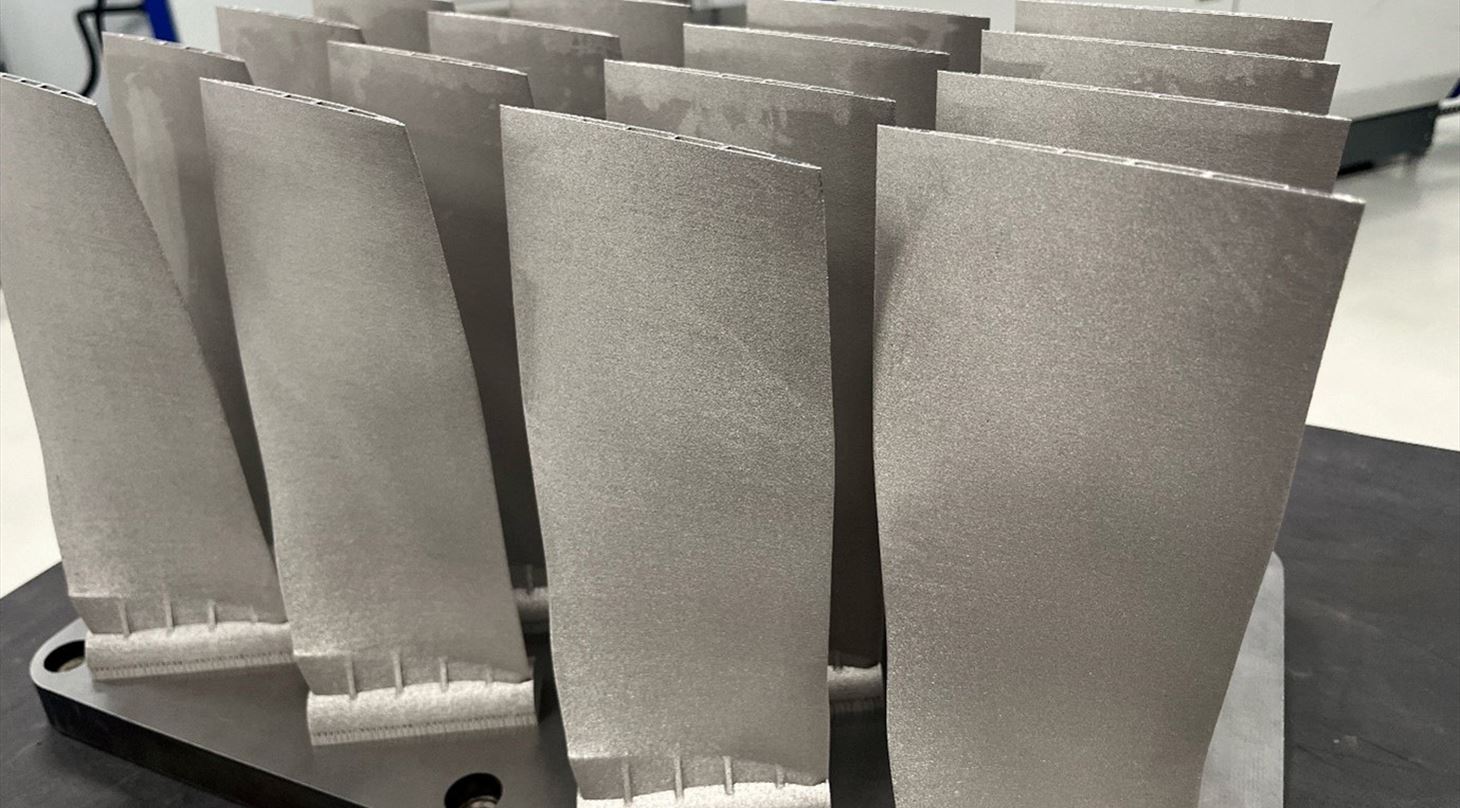
Faster drones with metal 3D printing provide a competitive advantage
Metal 3D printing provides lighter and therefore faster drones and a strengthened market position. This is demonstrated by a MADE project with Acodyne, where they received help from the specialists at the Danish Technological Institute to optimize the drone motors' fan blades by reducing weight.
With metal 3D printing, we have reduced the weight of the blades by 30 percent. This weight reduction has cascading effects, which can lead to an overall weight saving of 1-2 kg on the motor's fan disk, improving both the speed and response time of our products and giving us a significant competitive advantage
- Claes Nicolajsen, CTO at Acodyne
Imagine an oil rig far out in the windy North Sea.
If a critical part gets damaged, it may require spare parts from land. Such parts can take a long time to arrive. Acodyne's electric cargo drones solve this problem.
You might be familiar with the concept from Amazon's delivery drones, which fly smaller packages - up to a weight of 2.4 kg—directly to the customer's doorstep. The difference is that Acodyne's cargo drones are significantly larger, faster, can carry up to 200 kg, and cater to customers with hard-to-reach and remote locations. Whether it's an oil rig, a wind turbine, or a remote military post.
A drone capable of transporting 200 kg requires powerful motors. Acodyne specializes in this with their so-called electric ducted fans, which can be described as electric jet engines.
Acodyne wanted to improve and further develop these by using metal 3D printing. Therefore, they sought help in a MADE demonstration project with the Danish Technological Institute's 3D printing specialists.
- We expected that with metal 3D printing, we could significantly reduce the weight of our blades. At the same time, 3D printing gives us the flexibility to quickly adapt and develop new designs, which is crucial for a company like ours that is constantly evolving our products, says Mads Schnack, CEO at Acodyne.
Lighter blades with 3D printing
In the project, the Danish Technological Institute was tasked with optimizing the design of the blades using metal 3D printing. The blades were weight-optimized without changing the outer geometry.
- We redesigned the blades, made them hollow, and added internal ribs, which was necessary to maintain strength and stability. The blades were printed in titanium, which is a light and strong material. With these changes, we managed to reduce the overall weight without compromising the blade's structural integrity, says Magdalena Susanne Müller, consultant at the Danish Technological Institute, adding:
- 3D printing allowed us to implement a design that would have been difficult to manufacture using traditional methods. The result is a lighter component that can still withstand the forces it is subjected to at high speeds.
Lower weight, higher speed
Acodyne has achieved a weight reduction of 90 g per blade - or up to one kilo per engine - which, according to Mads Schnack, provides Acodyne with great value.
- When it comes to flying objects like drones and planes, weight is crucial. The lower weight of the blades will make our products faster in speed, but also quicker in reaction time. It is a significant competitive advantage, says Mads Schnack.
Even though the unit price is slightly more expensive compared to Acodyne's old blades, Claes Nicolajsen has no doubt that 3D printing is the right way forward for Acodyne:
- Considering the cascading effects, we expect to be close to break-even. We may have already achieved a gain, he says.
As we scale production—and as metal 3D printing becomes more widespread—we expect the price per unit to decrease further, making the technology even more cost-effective
- Claes Nicolajsen, CTO at Acodyne
Overview of benefits
- Faster iterations - it is easier to make new 3D drawings and print than to test conventionally by e.g. making new molds
- Titanium blades are more durable than traditional blades
- Superior uniformity in the weight and geometry of the blades
- 3D printed blades are easier to repair
- 3D printed blades are lighter - weight is app. 1/3 of the original, which saves up to one kilo per engine. This saves energy and makes it accelerate faster, so the drone has better maneuvrer authority.
About MADE demonstration projects
With a MADE Demonstrations Project, a small or medium-sized company can receive up to 100,000 DKK in support to solve a specific challenge in the company or test a new technology in production.
By being connected with the Danish Technological Institute, FORCE Technology, Alexandra Institute, or DAMRC, one gains access to the technologies, knowledge, and expertise necessary to address the specific challenge in the company. This can be within materials or production.
MADE demonstration projects are co-financed by the European Regional Development Fund and the Danish Executive Board for Business Development and Growth. Would you like to hear more about the opportunities to test and demonstrate new solutions in MADE? Please reach out to MADE - they cover all of Production Denmark.
This article is originally published by MADE