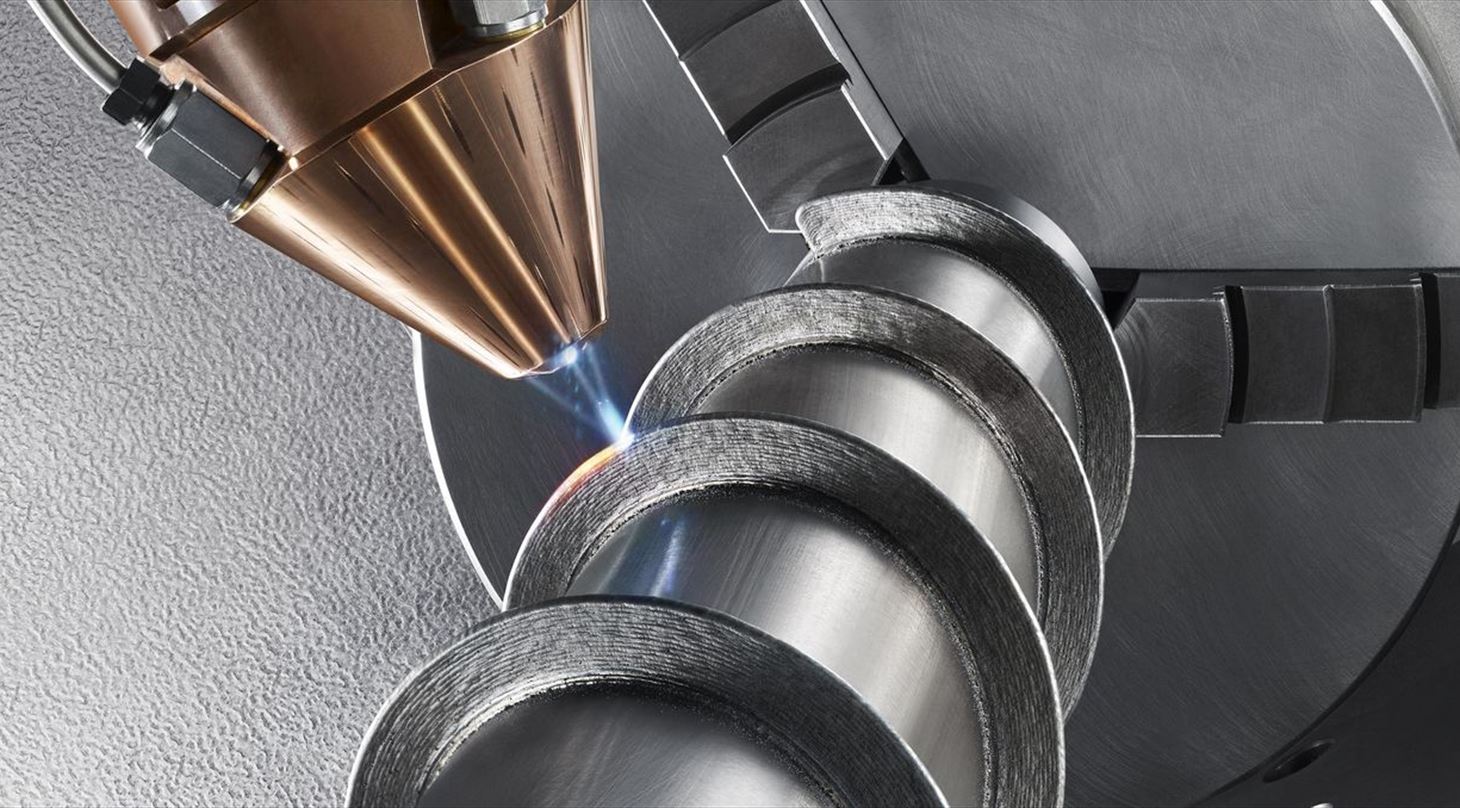
Directed Energy Deposition: A unique technology for repairing existing metal components
Directed Energy Deposition enables 3D printing of large metal components. In addition, the technology provides a unique opportunity to repair existing components - and this particular property allows for rethinking the production of components and companies' handling of repair tasks.
Directed Energy Deposition can be described as a mobile welding process, in which the energy source and the material are applied simultaneously to a component or plate, thereby creating a melt pool in the area where the material is applied.
- You can think of it as a movable print head that sits on a robot arm and where everything you need is there. This means that you have both an energy source and powder or wire, which can be controlled in relation to how the material is deposited. This gives fewer control restrictions than with e.g. Powder Bed Fusion, says Christopher Gottlieb Klingaa, Danish Technological Institute.
Online course in Directed Energy Deposition
Directed Energy Deposition is available with different types of control systems. These control systems can have a movable print head, a movable platform - or both. The movable control system, which deposits the material from different angles, provides additional possibilities in terms of design freedom and geometry, especially when the part can be angled in different directions with the movable platform.
Repair of existing components
Unlike powder sintering technologies, which take place in closed-loop printing systems, Directed Energy Deposition often has an open printing system that is ideal for 3D printing of large-scale components. This is often seen in the space industry, where Directed Energy Deposition is used for printing rocket parts. In addition, the open printing system also paves the way for the repair of existing components.
- It is significantly easier to repair existing components with Directed Energy Deposition compared to Powder Bed Fusion, and it is actually also one of the special things about the technology. If you were to repair a part in a powder bed, it would be a hassle because the material is all over in the form of powder. Here, it is easier to use Directed Energy Deposition, which in some cases almost works like an advanced glue gun, which applies the material where it is to be used, says Christopher Gottlieb Klingaa.
A profitable choice
With Directed Energy Deposition, the industry can take advantage of unique opportunities to repair assembled components. An example from the industry is wear and tear of large gears, where broken teeth are a common problem. Here, it is obvious to use Directed Energy Deposition as an alternative to buying a new gear, as the technology applies material to the places where the teeth are broken. After applying material, the gear will typically be machined to its specifications.
When it comes to material consumption, there is a potential for large savings. In addition, it is often better to repair than to manufacture a completely new component: Not only is it significantly cheaper, but it is also in line with the green transition
- Christopher Gottlieb Klingaa, Danish Technological Institute
"The big challenge is the level of detail"
Although Directed Energy Deposition is a technology with several strengths, it also has its weaknesses: Compared to Powder Bed Fusion and 3D-printed applications for the medical and food industries, Directed Energy Deposition differs significantly because the printing is coarser in all respects, and therefore the technology is best suited for large-scale components.
- The classic and highly detailed parts that you can make with Powder Bed Fusion cannot be made with Directed Energy Deposition. Likewise, you can only to a lesser extent make lattice structures, where the complexity and thickness of each element is limited because the Directed Energy Deposition process is coarser. This means that the major challenge lies in the level of detail, says Christopher Gottlieb Klingaa.
Opens up for centralization and local production
Faced with the question of what the prospects are for Directed Energy Deposition, Christopher Gottlieb Klingaa points to the possibility of centralizing companies' production and repair tasks.
- I think that companies will be able to catch up quite a bit in relation to the environment and the economy through lower logistics and material costs, he says and adds:
- We are seeing an increasing trend towards keeping production local and centralizing tasks, where in the past we have been used to globalizing everything. Therefore, I believe that Directed Energy Deposition can become part of the "toolbox" that companies will use to have a complete local production in the metal industry. Thereby, companies can both repair and produce locally without being dependent on the waiting time for critical components to be shipped.
Read about the other AM technologies
The Danish Technological Institute is ready to offer advice
If you as a company are interested in investigating the possibilities for implementation or 3D printing using Directed Energy Deposition, the Danish Technological Institute has a solid insight into the technology and will therefore be able to advise companies and establish connections between possible partners for implementation or printing.