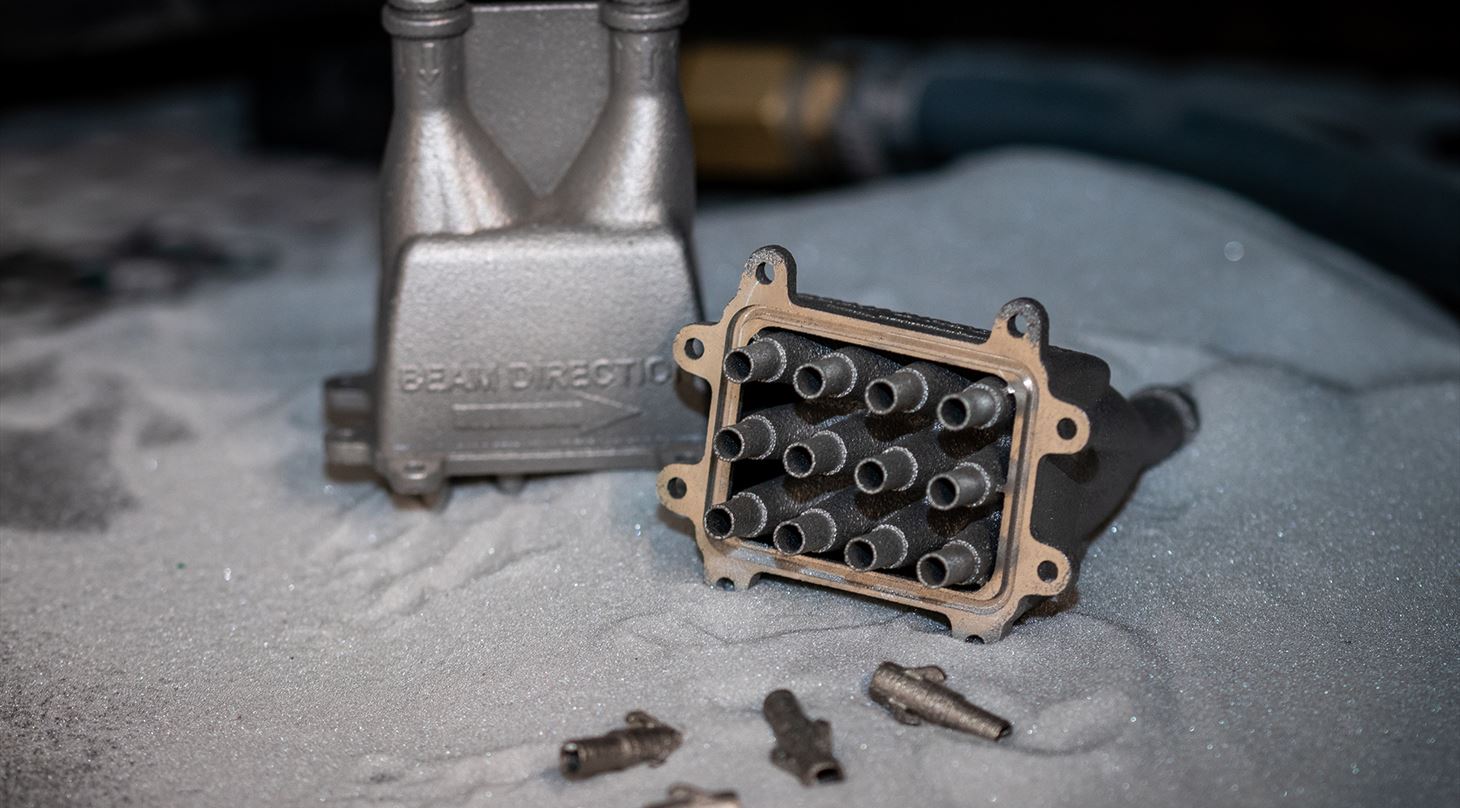
Compact cooling element was 3D-printed in aluminium
When JJ X-Ray had to develop a new cooling element for one of their instruments, a very compact solution with unhindered flow of water was needed. Due to the freedom of design and an attractive price at low unit numbers, 3D printing in aluminium was the perfect solution, and the parts - which were printed at the Danish Technological Institute - worked perfectly.
JJ X-Ray is a small Danish company that designs and manufactures high-end solutions for high-precision instruments, where great durability is also important. It could, for example, be equipment for scientific experiments, where the target groups are the research environments within analytical X-ray and synchrotron radiation.
These solutions are often very advanced, and there are high demands for the various components - for example in relation to vacuum tightness, surfaces, and tolerances. That was also the case when JJ X-Ray had to develop a new cooler for an instrument. The instrument was to be used for cooling a so-called White Beam Slit at Catereté Beamlinet at the Brazilian LNLS laboratory (Brazilian Synchrotron Light Laboratory), where the deposited power from an X-ray is up to 1500W.
Need for special properties
The cooler had to be developed from scratch, and it had to be very compact to fit into the instrument. At the same time, there had to be water flow with very little resistance – so naturally, it also had to be completely tight. This combination meant that a complex geometry was needed, and in addition, vibration damping had to be built into the nozzle ends.
Only a few of the coolers needed to be produced, and there was a focus on keeping the price down. That's why the designers at JJ X-Ray started looking at 3D printing.
3D printing was the (only) right solution
JJ X-Ray contacted the Center for Industrial 3D Printing at the Danish Technological Institute, which offers 3D printing in metal. Here, they received advice on the various options, and the Danish Technological Institute helped optimize the design that JJ X-Ray's development department had made, so that it could be printed at the lowest possible cost.
3D-printed aluminium was chosen, because it is relatively cheap compared to stainless steel and titanium, as you can print really fast, because aluminium quickly absorbs heat from the lasers. The small springs are printed in 316L stainless steel to keep the strength and elasticity high. As mentioned, the background was a desire to have a compact part with the least possible flow resistance, and with 3D printing you ended up with a simple solution that was easy to install because the elements could be assembled in one component. Should the cooler be made using traditional methods, there would be many different assembly points.
- Inside the cooler, the input and output flows run very close to one another in internal channels that fold into each other - a so-called manifold. This solution can only be made with 3D printing, and it helps to make the cooler extra compact, says Lasse Haahr-Lillevang, who is a 3D printing specialist at the Danish Technological Institute and has worked with the solution for JJ X-Ray.
The coolers were printed on the Danish Technological Institute's metal printers, and it was also ensured that the parts were given the right post processing to achieve the desired surface properties.
The whole component consists of three different parts - cooling head, nozzle heads, and a tube in between. The first two are printed while the tube was purchased to keep the price down, but the whole thing could also be 3D printed in one piece.
Cheaper than the alternatives
3D printing was a cheaper solution than traditional manufacturing because the number of pieces was very low (4 sets in total - 4 x cooling heads in aluminium and 4 x 12 springs in stainless steel 316L). But this particular solution would not make sense - or be possible - to make in any other way, because it is so compact and complex. Then it would have to be designed completely different. Thus, 3D printing offered the absolute best fit between high performance and low price, and the business case would still be good if 1,000 pieces were to be produced. At JJ X-RAY, they are also very satisfied with the solution.
With 3D printing, we had the opportunity to optimize water flow and strength in a very compact design, and it was not possible with a welded construction. Therefore, 3D printing was the right solution for us
- Jacob Navntoft, JJ X-Ray
The 3D-printed coolers are now in use with the instrument, and they perform as they should. However, JJ X-Ray learned in the assembly process that aluminium was a little soft for the purpose, so it was difficult to pack against the flange - but it succeeded. However, next time they will choose 316L stainless steel or titanium for the purpose.
In addition, the process meant that JJ X-Ray and not least the company's designers gained valuable experience with 3D printing, which they can use for future solutions, which need to be tailor-made and in small pieces.