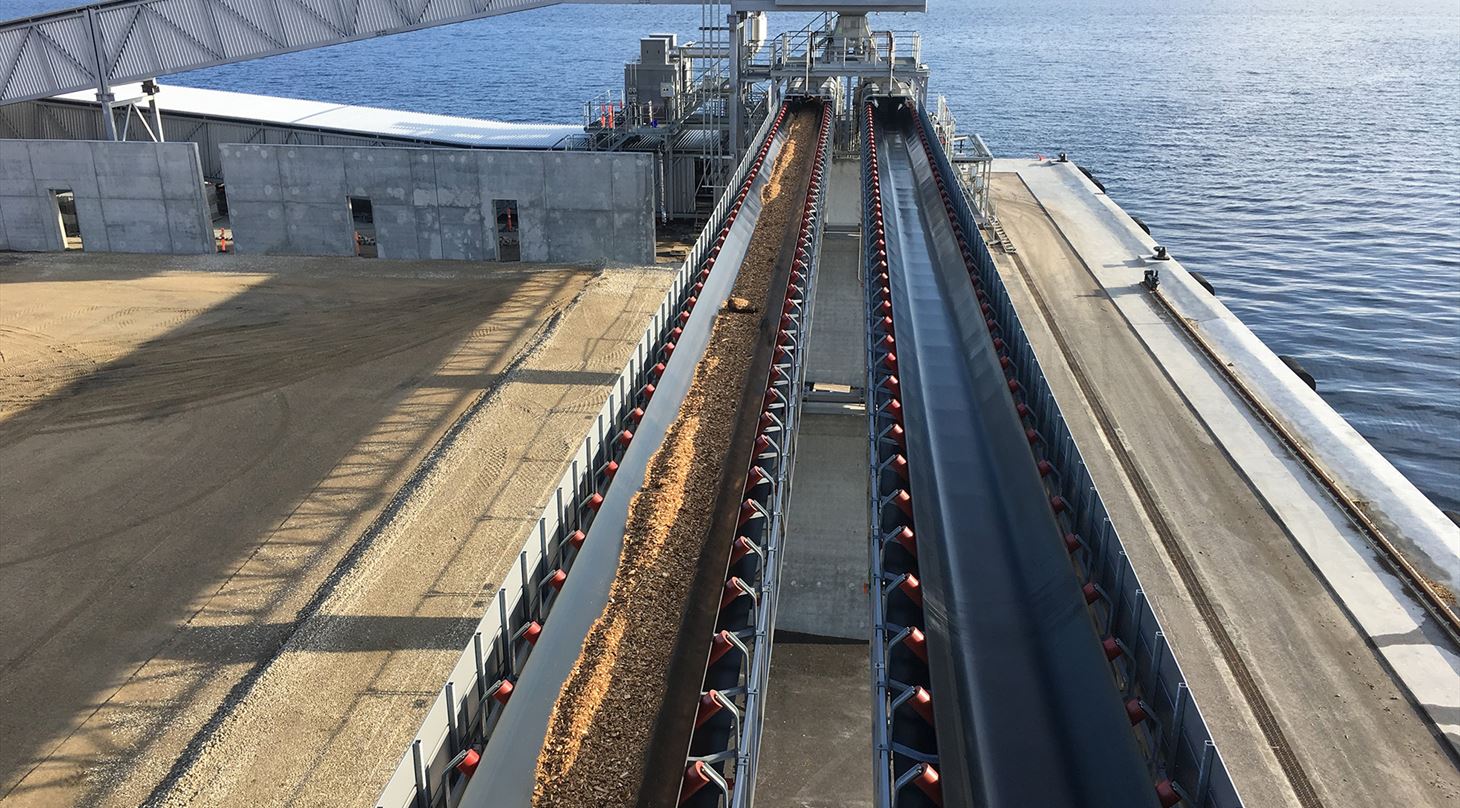
ATEX Inspection - ATEX on machinery still presents challenges
Select Page
Although it has been many years since the ATEX directives came into force, we still see brand new plants where machines and equipment are not certified for use in areas with a risk of explosive atmospheres. The lack of knowledge of the directive's requirements can result in large costs for both the manufacturer and the end user.
- Both we and our colleagues in the industry still find plants that do not meet the applicable ATEX requirements when we carry out the statutory inspections of machine plants that work with explosive atmospheres, says Frits Fynbo, business manager and ATEX specialist at the Danish Technological Institute
The deficiencies typically relate to machines, mechanical equipment, and safety systems. On the other hand, there are fewer errors in the electrical equipment, where the requirements for the Ex marking have been known long before the ATEX directives came into force.
The principles for CE and Ex marking of machines that work in or with an interface to explosive atmospheres - e.g. a belt or screw conveyor - are the same as for electrical equipment.
- Today, no electrical installer would dream of installing an electric motor in an explosive atmosphere if it is not Ex-marked – that is also where we need to get to when we think of mechanical equipment, says Frits Fynbo
Lot of excuses – but no good ones
The belt conveyor is a typical example of mechanical equipment that is delivered without Ex marking, even though it has an interface to explosive atmospheres in, for example, the interchange between two conveyors or for the loading for unloading trucks.
When the manufacturer is confronted with the lack of Ex marking, a long list of excuses follow - e.g. that antistatic rubber bands are used, low speeds etc. But the requirement is that all potential sources of ignition must be risk-assessed and handled according to the zone that the facility has interface to – e.g. category 2D for zone 21.
For a belt conveyor, this means that hot surfaces which can occur due to misalignment, blocking, bearing faults etc. must be assessed under foreseeable faults. Here, it may turn out that there is a need for a safety system for checking the ignition sources according to applicable standards.
It must be clear from the Ex marking and the associated declaration of conformity that these assessments have been carried out and that the machine meets the requirements of the ATEX directive.
In addition, the nameplate must show which category, dust group, temperature class etc. the belt conveyor meets - and thus which zone it may be used in. This is exactly what is checked during an ATEX inspection.
- Another good example of using misbranded or outright wrong equipment is the cell lock. Here, we often see that cell locks are Ex-marked correctly, but that they are not approved as a safety system, even though they are used as barriers against pressure and flames from an explosion in, for example, a filter plant. In order for the cell lock to be used as a barrier, it must be certified by a notified body, says Frits Fynbo.
Risk of delays
Machines, equipment, and material manufactured after June 30th 2003 and used in or with an interface to explosive atmospheres must not actually be put into use if it does not meet the requirements of the ATEX directive.
This means that if errors and deficiencies are not found before the statutory initial inspection, which is carried out immediately before the plant is handed over to the end user, it will cause delays in connection with the replacement of equipment, changes in the control, etc.
Focus on ATEX reduces expenses
A greater focus on the ATEX requirements for mechanical equipment will help to minimize both costs and delays in the projects. This focus is achieved by the end user clarifying the requirements in the tender material and getting the manufacturer to accept the requirements through the contract.
- We also recommend that an impartial inspection be carried out while the facility is under construction. That way, the manufacturer becomes aware of any errors and deficiencies as early in the project process as possible, Frits Fynbo concludes.
There is no requirement for the manufacturer to use a third party to carry out the statutory initial inspection, but it can be useful to write it into the contract so that the end user can ensure impartiality.
Facts about the requirements of the Machinery and ATEX directives:
- Machinery that works with explosive atmospheres must be risk assessed in accordance with EN 1127-1
- Equipment located in or with an interface to explosive atmospheres must comply with the ATEX directives and be Ex-marked
- Electrical and mechanical installations must comply with EN 60079-14
- Before commissioning the machinery, an initial inspection must be carried out in accordance with EN 60079-14 and -17