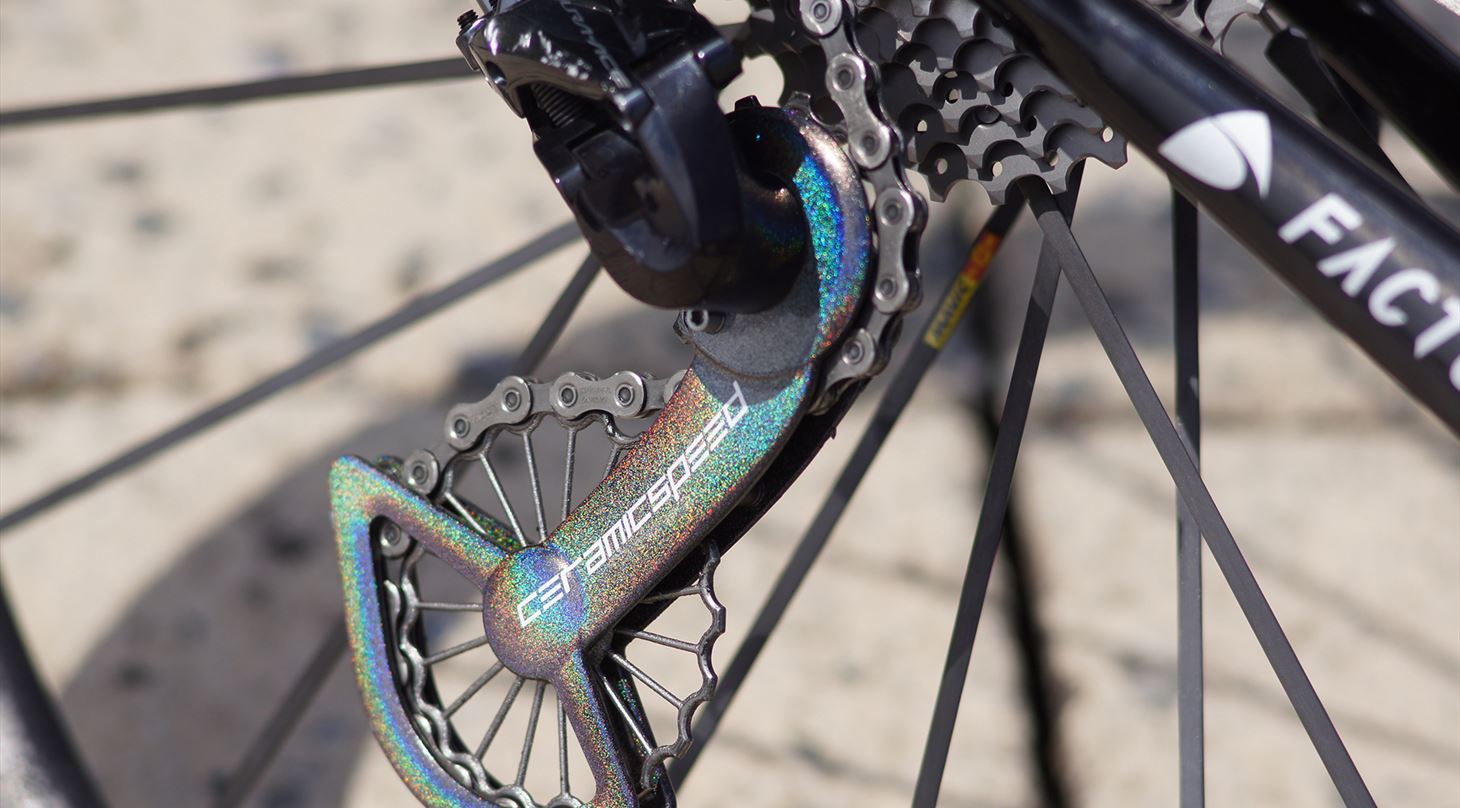
Additive manufacturing revolutionizes race cycling - Innovative, 3D-printed pulley wheels increase performance
Cycling applies the same lightweighting requirements as the broader mobility sector and long-haul races, like the 3,460 kilometer Tour de France, offer unique engineering challenges to optimize weight while maintaining resiliency across the over course of the race. In cooperation with the selective laser melting experts at the Danish Technological Institute, the cycling innovating company CeramicSpeed developed a lightweight, yet durable pulley wheel used by professional cyclists for improved performance.
The global cycle market is driven by innovations and to stay at the forefront of the industry CeramicSpeed, who revolutionized races by introducing ceramic bearings to professional cycling, entered into a partnership with the Danish Technological Institute (DTI). With a quad-laser SLM®500 and twin SLM®280 system, the institute has been successfully utilizing selective laser melting for years, making them the perfect partner to optimize development. The results yielded the world’s lightest gear wheel, the so-called titanium pulley wheels, developed by the partners working together for race-condition testing from professional riders racing in this year’s Tour de France.
- 3D printing technology has given us a lot of leeway to experiment creatively with design, while at the same time being able to optimize a product’s function, Carsten Ebbesen, R&D Manager at CeramicSpeed stated. The collaboration with DTI has led us to develop and produce gears in a radically new design form that is only possible with 3D printing.”
Built in titanium on the SLM®500 metal additive manufacturing machine, the pulleys are equipped with 17 spokes with a diameter of 2 mm and a wall thickness of only 0,4 mm. Due to the hollow design, it has been possible to reduce the total weight of the sprocket to 8,4 grams. Thor Bramsen, Industrialization Manager at the Danish Technological Institute is enthusiastic about the possibilities of the SLM® technology:
- The hollow geometry of the objects cannot be produced with conventional methods, and the 3D printing in combination with subsequent specialized processes leads to a unique innovative product. Despite the complex geometry, DTI is able to reliably build the same quality parts in series production.
The gears produced with the selective laser melting process have also withstood rigorous tests to prove their quality. The pulley wheels are placed on the outer gears in the gearshift and are thus subject to wear. CeramicSpeed’s R&D department have been testing the wear on the printed titanium parts, which proved to be more durable and suitable for corrosion resistance and strength at low density than traditional aluminium parts.
To offer serial production of a high-quality, additively manufactured product, the entire process chain must be coordinated. This includes the robust, reliable, additive manufacturing machines from SLM Solutions, but the process begins with the component redesign for the additive process. The product design from CeramicSpeed was optimized by DTI for series production with additive manufacturing technology. This process is a delicate mix of not changing the customers design, while adding material for surfaces that require CNC machining, optimizing support, and minimizing wall thickness and weight. After successful production, the equally challenging, yet important post-processing steps take place, where the Danish Technological Institute uses its entire range of manufacturing knowledge, ensuring that only assembly is required when the finished product is delivered.
The first ceramic bearings from CeramicSpeed were introduced to the Tour de France less than 20 years ago. The innovation of design provided by selective laser melting, and their partnership with the production experts at the Danish Technological Institute, help the company continue to push boundaries of cycling technology and are helping set new standards as riders test the latest innovations in their training to be the next to debut new advancements at future Tour de France races.