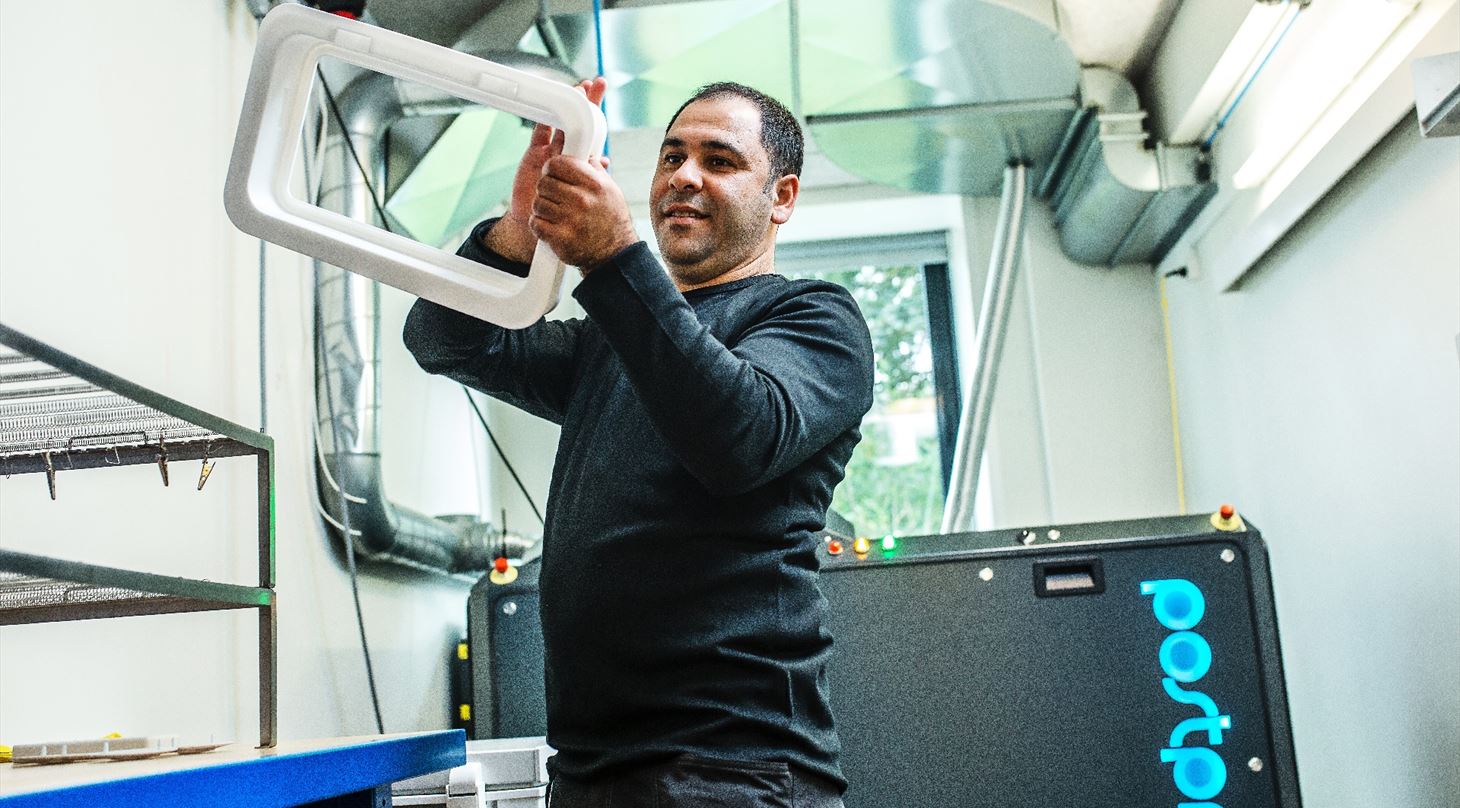
Post-processing of 3D printing needs to be fully automated
The Danish Technological Institute, Scape Technologies, and the British company AMT aim to fully automate the post-processing of 3D printing in a new EU-supported project called DMS Nextgen.
Industrial 3D printing is a digital production technology where a large part of the production process is controlled online. However, the post-processing of the printed components still involves a series of manual processes. Together with Scape Technologies and the British company AMT, the Danish Technological Institute is now attempting to fully automate this process in a new EU-supported project called DMS Nextgen.
Production, handling, and post-processing
In recent years, the Danish Technological Institute has established a complete setup for industrial 3D printing production in both metal and plastic. This setup includes the digital processes preceding the 3D printing process itself and the post-processing steps that finish the 3D-printed parts. It is precisely the post-processing of theparts that primarily requires manual handling.
- In plastic powder 3D printing – the so-called Selective Laser Sintering technology – the parts are removed from the build chamber once they have cooled down, so most of the powder can be removed from the parts. Subsequently, the parts are cleaned of the remaining powder before they receive a surface seal if there are specific requirements for the hygiene and cleanliness. All of these processes require manual handling, explains Anders Bæk Hjermitslev, Team Manager at the Danish Technological Institute.
Automation of the processes
Now, the Danish Technological Institute will attempt to automate the processes in a new EU-supported project called DMS Nextgen. The project will develop a fully automatic solution that can perform all the steps in the post-processing of the parts after 3D printing production. This includes cooling, unpacking, cleaning the parts, and finally sealing the surface of the parts. The plan is to use a conveyor booth and robot(s) to move the parts between the different process steps in this solution.
The project is being carried out in collaboration with the Danish software automation company Scape Technologies, which specializes in robot-automated material handling – known as bin-picking. In the project, Scape Technologies will provide technology for 3D visual recognition, advanced gripping technologies, and robot control to handle and transport the 3D-printed objects between the modules in the solution.
- Automating the post-processing of 3D-printed objects presents some very interesting challenges, even with the experience and technology already available. One of the primary challenges is recognizing a 3D-printed object and determining the object's orientation within a batch of objects that can have different designs, and where the object's shape is not yet detailed due to residues left by the 3D printing process. The combination of these elements will challenge the recognition process in ways that we are not normally confronted with. Secondly, the gripping technology itself and the handling of diverse 3D-printed parts within a single batch require special considerations when regular requirements for precision grip and handling speed need to be maintained, says Carl Johan Danbjørg, Development Project Manager at Scape Technologies.
The British Sheffield-based company Additive Manufacturing Technologies (AMT) will produce equipment for the post-processing of 3D-printed parts.
At the end of the project, the entire system will be integrated, and the demo solution developed in the project will subsequently be placed at the Danish Technological Institute.
About DMS Nextgen
DMS Nextgen is a Eurostars project with a total budget of nearly 1.1 million euros. Eurostars is part of the Eureka network, co-financed by the EU through Horizon Europe – in Denmark, the project is financed by Innovation Fund Denmark.
The project runs from January 2024 to September 2025. The project partners are the Danish Technological Institute, AMT, and Scape Technologies A/S.