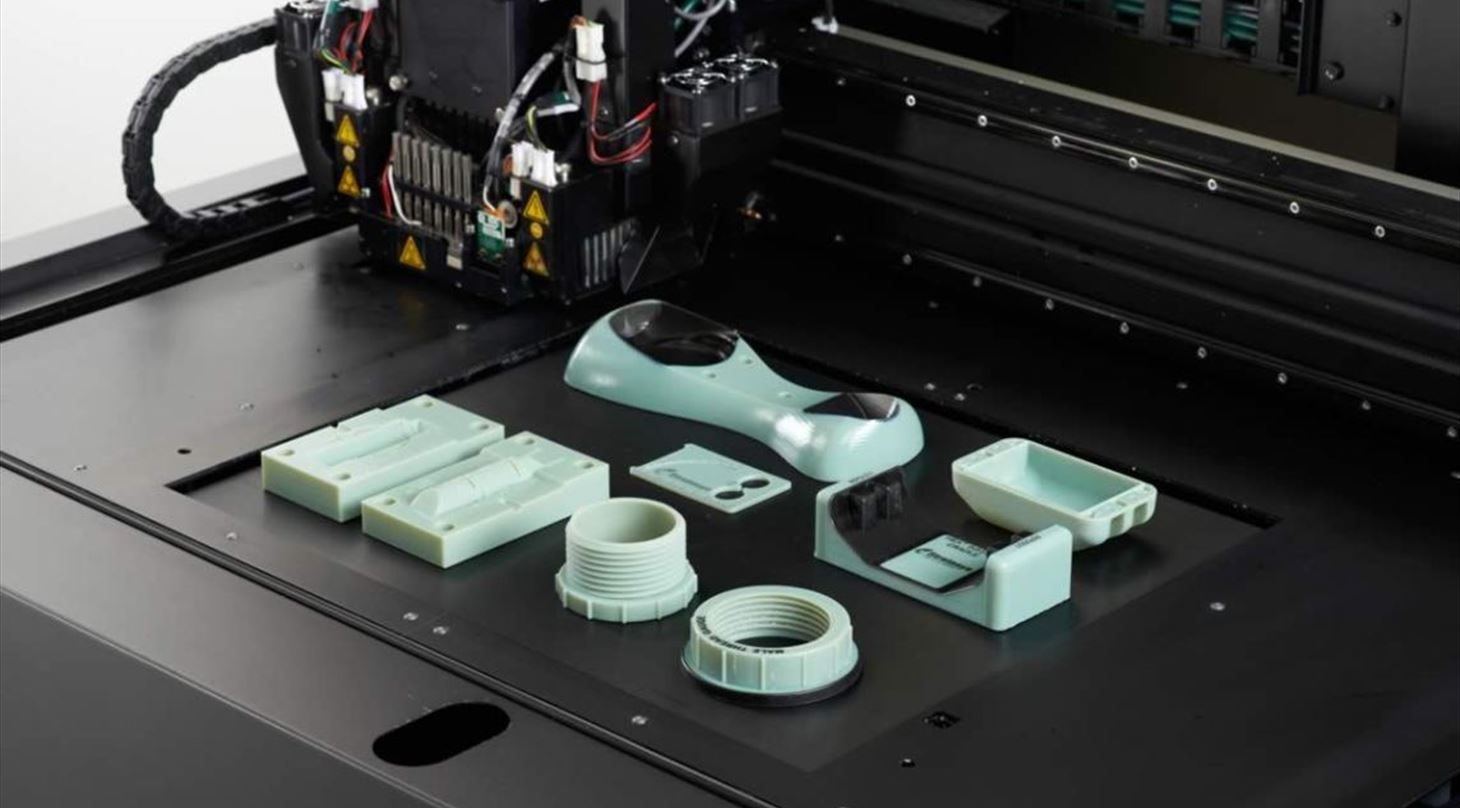
3D printing with Material Jetting - get the most accurate and realistic prototypes
Material Jetting is a great choice of 3D printing technology if you want prototypes with colours and a high level of detail. In fact, the technology is currently considered to be the most accurate form of 3D printing, and therefore it is suitable for companies that want to have realistic prototypes early in the development process.
The way Material Jetting works is that a print head consisting of several small nozzles drips resin onto a building platform. Immediately after the resin droplets have hit the building platform, the resin is cured with UV light, after which the building platform is lowered. Next, a new layer of resin is applied, which hardens, and this process repeats until the given part is finished.
Try our online course about Material Jetting
- When the nozzle drips the material onto the platform, it moves in some long paths depending on where the part is placed. Therefore, it is also very much about the placement of the parts in the path. This has a huge impact on how fast the machine can print the parts, says Sigurd Vigen Pedersen, consultant at the Danish Technological Institute.
High precision and accuracy
Since the printing takes place by a nozzle running in long paths, the printing process is not the most efficient when it comes to speed and time. On the other hand, the dripping method ensures that you get parts with high resolution and great accuracy - in addition, it is possible to make parts with colours and very small and fine details. Therefore, Material Jetting is today considered to be the 3D printing technology that has the highest precision.
Another advantage is that the printing process itself takes place at low temperatures. This has a positive impact on the accuracy of the parts.
- Compared to other 3D printing technologies, Material Jetting has a very low temperature in the build chamber, which is around 30-60 degrees. This means that there is not a very high risk of residual stress, shrinkage, or deformation in the parts during the process. At the same time, it is something that has a great influence on both precision and tolerances, Sigurd Vigen Pedersen explains.
Support material determines the surface finish
Like most other 3D printing technologies, there is a need for support material when printing with Material Jetting. However, before adding support material to your part, be aware that the use of support material gives a matte surface finish.
- You can either get a completely smooth and glossy surface or a matte surface when printing with Material Jetting. The surface depends on whether there has been support material or not: If you want the matte surface, you add support material on all the outer surfaces and dissolve it afterwards. If, on the other hand, you want a glossy surface, you can only get it where there has been no support material, says Sigurd Vigen Pedersen.
The video below from Hubs shows the Material Jetting printing process.
Should you add more support material?
Before choosing whether or not to use support, it can be important to consider the various pros and cons. One of the benefits of printing with support is that it allows you to create complex parts. Another benefit is that support material can be removed without any problems.
- Since you can print with several types of materials with Material Jetting, the technology also allows for dissolvable support material, which can be easily dissolved after printing, says Sigurd Vigen Pedersen.
Before adding massive amounts of support, however, it is worth adding that the material is printed solidly. This means that more material is used, which is already very expensive - and for the same reason, the costs in the printing process will also increase significantly.
A sure winner on the visual appearance
In 3D printing, you often distinguish between visual appearance and functionality - and here Material Jetting is a sure winner on the visual appearance.
Where the technology really differs from other 3D printing technologies is that you can mix materials in one part, and at the same time it is a very precise technology. In addition, you can make transparent parts and print with elastomers, which are flexible and rubber-like materials
- Sigurd Vigen Pedersen, Danish Technological Institute
Furthermore, it is possible to print different parts with different materials simultaneously on the platform, just as the technology can also print 'digital' materials. Digital materials mean that different types of resin are combined in one part. It is also possible to print mixed parts, i.e. parts consisting of different components. That way you avoid having to assemble several components after printing.
Faster development process with precise prototypes
The potential of technology to combine materials in one print also opens up the possibility of combining different hardnesses and colours - and this can be a significant advantage for companies that make consumer products. Companies often need to see the visual product and possibly identify and correct errors or make improvements before the product is put into production.
- It could, for example, be with a remote control that has both soft buttons and a hard plastic material around it. Often, in the development process and design phase of a new remote control, it will be necessary to make a prototype to see how it feels in the hand and how it feels to press it. Then you can print it in the right colours and materials with Material Jetting, so it will look like the product you will need in the end, Sigurd Vigen Pedersen explains.
The material properties lag behind
Although Material Jetting really performs on the visual appearance, the technology lags when it comes to functionality. The reason for this lies in the material properties because the parts are often not strong or durable enough for use as end components. This is partly due to the fact that the technology prints with thermosetting plastics.
- Since we are dealing with thermosetting plastics, they are often more brittle materials. Of course, you can get some materials that have good properties, but they are often more exposed. If you expose them to UV light, your part will, for example, change over time, says Sigurd Vigen Pedersen.
Read about all the AM technologies
Although the parts are UV-sensitive and get worse over time if they are exposed to sunlight, it is possible to make a few improving measures: For example, it is possible to give the parts finishing in the form of either a varnish or coating if you need to use your part functionally or want to use it outdoors.
The future for Material Jetting
As for what the future holds for Material Jetting, Sigurd Vigen Pedersen estimates that more companies will continue to use the technology for the prototype stage, where it is already being used to a great extent.
In relation to the development, I believe that it will take place within materials, where there will be even more and better materials
- Sigurd Vigen Pedersen, Danish Technological Institute
- At present, it is not the 3D printing technology that attracts the most attention. This is because most companies predominantly focus on other 3D printing technologies that are better suited for industrial use. Here, the great potential lies in powder-based 3D printing, where a lot of development is taking place, says Sigurd Vigen Pedersen.
The Danish Technological Institute offers insight into Material Jetting
If you as a company are interested in hearing more about Material Jetting technology, the Danish Technological Institute offers an online training course on Material Jetting and several other 3D printing technologies, where, among other things, the printer process, material types, and advantages and disadvantages are reviewed.