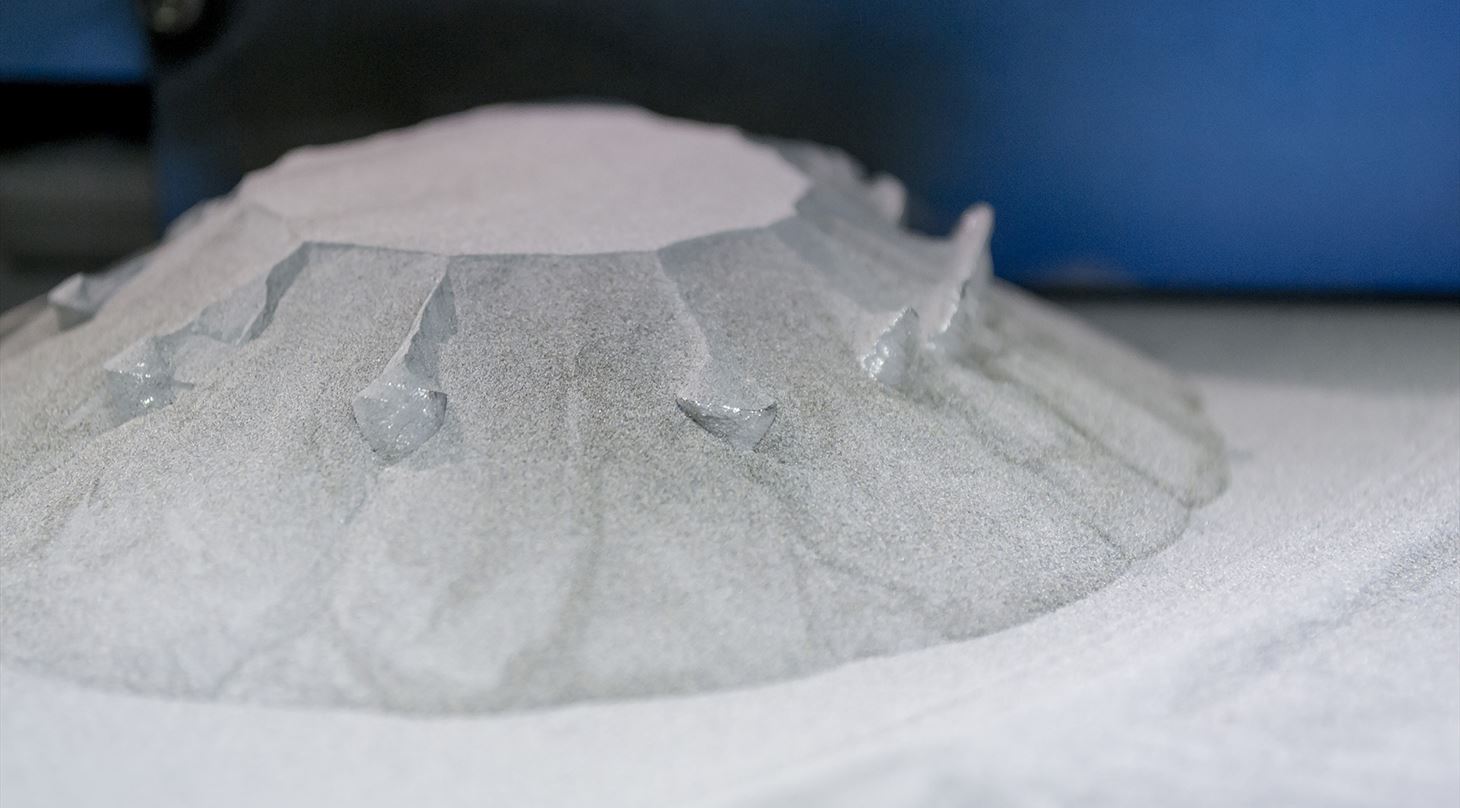
New and exciting materials for 3D printing - what is coming and what is trending
Material development in 3D printing is an area that attracts great interest. That is because a successful 3D print not only depends on the machine you use for printing - it also depends to a large extent on the materials you use. BUT the material world can seem huge and often unmanageable, and it can be difficult to stay up to date. Here, we try to create an overview of some of the many exciting plastic and metal materials in the world of 3D printing.
All manufacturing technologies have some material limitations. Just as you cannot cast or mill in all materials, you cannot 3D print in all materials. On the other hand, a lot is happening right now in the development of materials for 3D printing - and we’re seeing new materials almost daily. In order to live up to the noble art of restraint, we have chosen to concentrate on plastic and metal materials in this article.
Plastic or metal? How to choose the right material
Plastic and metal are both good and solid types of material, each with its own advantages and disadvantages. If we look at the strength side, then metal materials are superior. If we look at price and degree of processing, the plastic materials come out on top. In short, it takes more to in metal than in plastic.
Metal 3D printing requires a higher degree of specialized knowledge - especially around process control - and there are greater demands on machines and post processing equipment as well as the energy required to produce. That said, these extra degrees of complexity are often worthwhile as metal can produce some very complex geometries using materials such as stainless steel, aluminium, titanium, Inconel etc. Metals often have a significantly higher performance than plastic, and with the design freedom offered by 3D printing, printed metal materials can create some impressive results.
- When companies must decide which materials they want to use for their parts, they should assess the function of the part first - and look at the needs of the part. Should it be strong, light or heat conductive? What should it be able to do? What function should it perform? This is often where you can gain something if you already in the development consider the material based on the function. But it requires a change of mindset. Ideally, one would think function and then select material on that basis, says Lasse Haahr-Lillevang, Industrial 3D Printing consultant at the Danish Technological Institute.
When are materials suitable for 3D printing?
A usable material for 3D printing must be able to withstand the printing process. When you build a part with a laser - which is one of the technologies often used for 3D printing in both plastic and metal - the material melts, after which it solidifies. In that process, the material contracts, and it produces some enormous stresses, which can result in deformations or microcracks throughout the part. For a material to be suitable for 3D printing, it is therefore an important quality that it can be melted and regain shape without severe challenges.
Historically, you have taken the materials that are already used in the industry, and which in principle can be printed because their qualities are known. But there is a huge potential if you are willing to look into materials that have been developed specifically for 3D printing.
- In the industry, you would prefer to work with the materials you know in advance – e.g. stainless steel, which is fine to print in, but which is not developed for printing. Consequently, there are some benefits that are not utilized, but that are ‘ripe for picking’ That is precisely why you should look at the function first and determine the material based on it, says Lasse Haahr-Lillevang.
Alloys provide new quality
The number of known alloys on the market is growing steadily as the market generally grows, but there is now a greater degree of material development specifically for 3D printing. For example, Uddeholm has developed a tool steel, AM Corrax, which is very corrosion resistant. In aviation, where weight is paramount to the function, for instance, Scalmalloy, developed by APWORKS, has entered the market, where scandium has been added to aluminium to make lightweight aluminium very strong. Another type of material optimization is from Elementum 3D that has developed Metal Matrix Composits (MMCs) for 3D printing – here, they have added a ceramic material to known alloys to increase the performance of the alloys, but also to be able to print in the strong aluminium alloys. The ceramic additives have been shown to stabilize the printing process so that some of the high-performance aluminium alloys (A6061, A2024, A7050) have become available.
Meta-materials - what is that?
Meta-materials are when you have a material, and through design and structure – e.g. a lattice structure or a porous structure - design yourself towards different properties. Via lattice structure, you can make something that is light and strong, or something that breaks and quashes in the right way - many features can be built into a part through meta-materials.
The qualities of the part therefore depend not only on the material used but also on the structure in which you choose to build the part. It is a large area of research, but it is very rare that we meet designers who design with lattice structure in mind. It is often the outer geometry that you focus on, but it is important to also remember the inner structure, as you can achieve other functionalities
- Lasse Haahr-Lillevang, Danish Technological Institute
For example, using a lattice structure, you can make a part shock-absorbing or vibration-absorbing, as can be seen in this case from the cartridge manufacturer Ortofon.
New and upcoming materials
There are a lot of new materials on the way, and many of them are very exciting. Especially in the field of alloys and meta-materials, there is a huge development.
- It’s like we haven’t even started yet - there is so much more to discover, concludes Lasse Haahr-Lillevang.
The table below gives an overview of some of the different materials - both the existing ones and those that are coming.