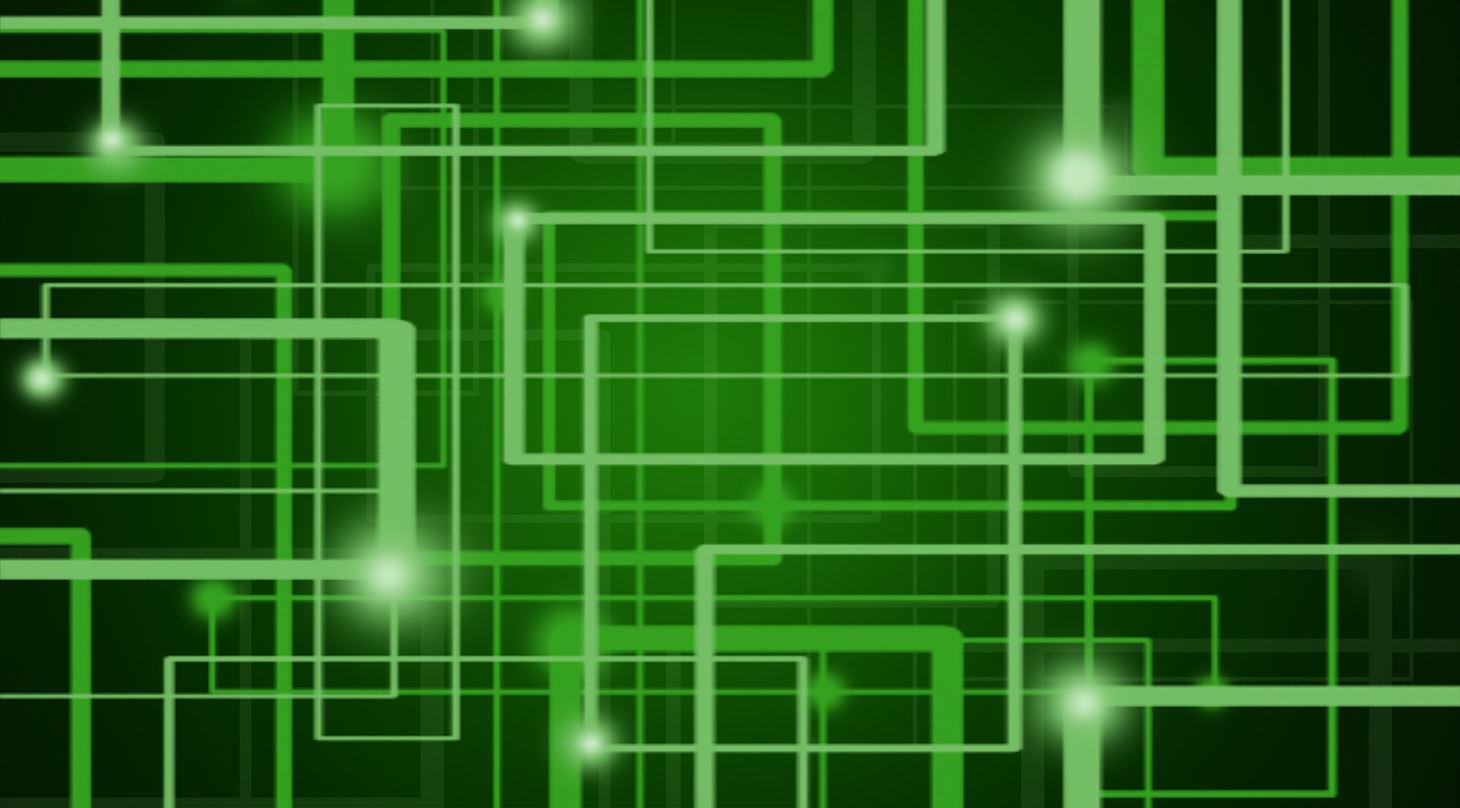
Is 3D printing a green technology - and when?
3D printing has great potential to help the green transition on its way, but it is important to distinguish facts from fiction and focus on where the real value lies. Here, Jeppe Byskov from the Danish Technological Institute does just that, and he focuses on concrete green applications - and warns against painting too pretty a picture.
The green transition is high on the agenda in several Danish industries - and rightly so. CO2 reduction, energy optimization and green initiatives are a joint task, and it requires a joint effort if we are to achieve the Danish goals of reducing CO2 emissions by 70% by 2030. In this connection, there is a lot of talk about 3D printing technology contributing to the green transition - and there is no doubt that it can.
Unfortunately, there are many (undocumented) postulates flying around, and there is a tendency for those who shout the loudest to be heard the most - this risks overshadowing the real potential and not least the fulfilment of it. For example, we often hear that 3D printing is a very green technology because you can produce locally and only use the amount of material involved in the process. This is definitely not wrong, but it is a very fragmented image that is presented, where you look at a very small part of the potential.
First: focus on facts
At the Danish Technological Institute, we have a strong focus on documenting why 3D printing is a green technology– when it is and when it is not. Is it, for instance, in the manufacturing itself, or is it more in the use of the 3D-printed component? And what can we do to make the technology even more sustainable? These are interesting questions to explore. Right now, there is still a lot of uncertainty, and we want to get closer to something fact-based. We are obliged to do so due to our position and our experience - to be those who consider the entire value chain and conclude on a scientific background. This could, for example, be through life cycle analyses of specific products throughout their lifetime.
Let us help you with 3D printing production
Ultimately, I would like us to get a label within manufacturing that shows how energy efficient the manufacture of a component is - in the same way as, for example, refrigerators have an A, B, C label. I sense that this aspect is important to many companies; it's not just the price but also how sustainable the product is. Companies such as LEGO, Grundfos and Danfoss have dedicated goals of being CO2-neutral or reducing their emissions, so this means that they look at emissions when manufacturing or operating components - if not to the same extent as they look at the economic aspects, then very close. We would like to help support this development.
3D printing streamlines operations
At the Danish Technological Institute, we assess that the biggest benefit of 3D printing lies in the operation - the fact that we can manufacture components with a significantly higher performance. The classic example is conformal cooling, which is used for cooling e.g. tools and motors, or for higher-performance nozzles for aircrafts. Here, you can achieve some very direct energy improvements with 3D printing, and since the operation typically lasts for many years, the primary energy profit is achieved here.
Weight optimization is another good example where e.g. the aerospace and automotive industries can achieve large fuel savings in the long run. Perhaps it is a little more surprising that heat exchangers and heat sinks can also be optimized with 3D printing, but this is an area we are focusing on. Among other things in the Easy-E project, where we take a handful of industrial products from different industries and show that we can make completely new business cases and energy improvements using topology and design optimization.
A Danish report from EA Energy Analysis confirms that there is great potential in energy efficient solutions - not just the 3D-printed ones. Here, it is stated that this type of solution can save society an extra bill of about DKK 14 billion towards 2030, where the goal of a 70% reduction in CO2 emissions must be met.
Green transition, black bottom line – the good examples
As mentioned, it is in the field of energy efficiency that I see the great potential for 3D printing. The technology provides the greatest value when we consider optimized product functionality. With design freedom and a short development time, 3D printing offers several opportunities to create more energy efficient products, which not only provide gains on the bottom line, but which also support the green transition. Here are three concrete examples:
- Energy and power optimization: With 3D printing, you can create freely designed internal channels, because the 3D printer does not care that the geometry becomes more complex. This means that you can e.g. make heat exchangers, cooling plates or hydraulic blocks that are smaller, lighter, and more efficient. For example, we have re-designed a hydraulic system for 3D printing, where we completely avoided 90-degree angles in the internal hydraulic flows. In this way, the pressure drop was reduced by 25 percent, while the weight and volume were lowered by 95 and 90 percent, respectively.
Topology optimization: With topology optimization, all the material that does not matter to the properties of a part is removed, leaving you with a bone-like structure. This allows you to further reduce material consumption, so that the print time is shorter, which means that the price is lower. Together with Boeing, we have previously done topology optimization of an aircraft component, which led to a 35 percent weight reduction - from 310 to 200 grams. At the same time, the optimization meant that the component was less stressed due to better stress distribution. It also resulted in more sustainable flight, as the weight reduction improved fuel economy by 2 million Euros over the life of the aircraft, while reducing CO2 emissions. Similar benefits could be achieved in the manufacturing industry. 3D printing has also meant that Boeing can manufacture spare parts on site and on demand, so that they avoid waiting time and reduce stockpiling, and this leads to my last example.
- Precise part numbers: With 3D printing, you can avoid waste production and large stockpiling by producing more accurate part numbers. The production flexibility is great, and both the conversion and delivery time are short, while the price does not get noticeably higher with smaller series. This can be especially beneficial for smaller businesses that can run on-demand production or use 3D printing in the ramp-up process.
The potential is there - but remember the whole calculation
Let us briefly return to the example of reduced material consumption and local production, which I mentioned at the beginning. It is true that in the actual production, you only use the material that is included in the product as opposed to e.g. milling, where you mill a large percentage of the block away - so that is positive. BUT if we look at the powder-based 3D printing methods, which are very common for industrial use, then it is very energy-intensive to make the powder.
You start with a solid material, which you then melt and bombard with particles, whereby it becomes powder. The powder must then be fused together again in the 3D printer to the desired part - so it is both back and forth to end up in the same place. This ideal energy-wise, and we must take this into account when we make the big calculation in terms of how energy efficient a 3D-printed component is.
Then there is the potential for more local manufacturing, where we can sell or distribute digital files and manufacture parts on 3D printers locally. If we hold it up against the extreme opposition, where the raw material is extracted in Africa, sent to China for production and then sent to stock in Europe and then sold to the United States, then it is true that there is potential. But that potential also exists with more traditional manufacturing methods, so it is not unique to 3D printing.
But the good - and unique - advantages are there, and at the Danish Technological Institute we have already seen several companies create value and competitive advantages through energy efficiency with 3D printing. So just start thinking green - it can quickly pay off.