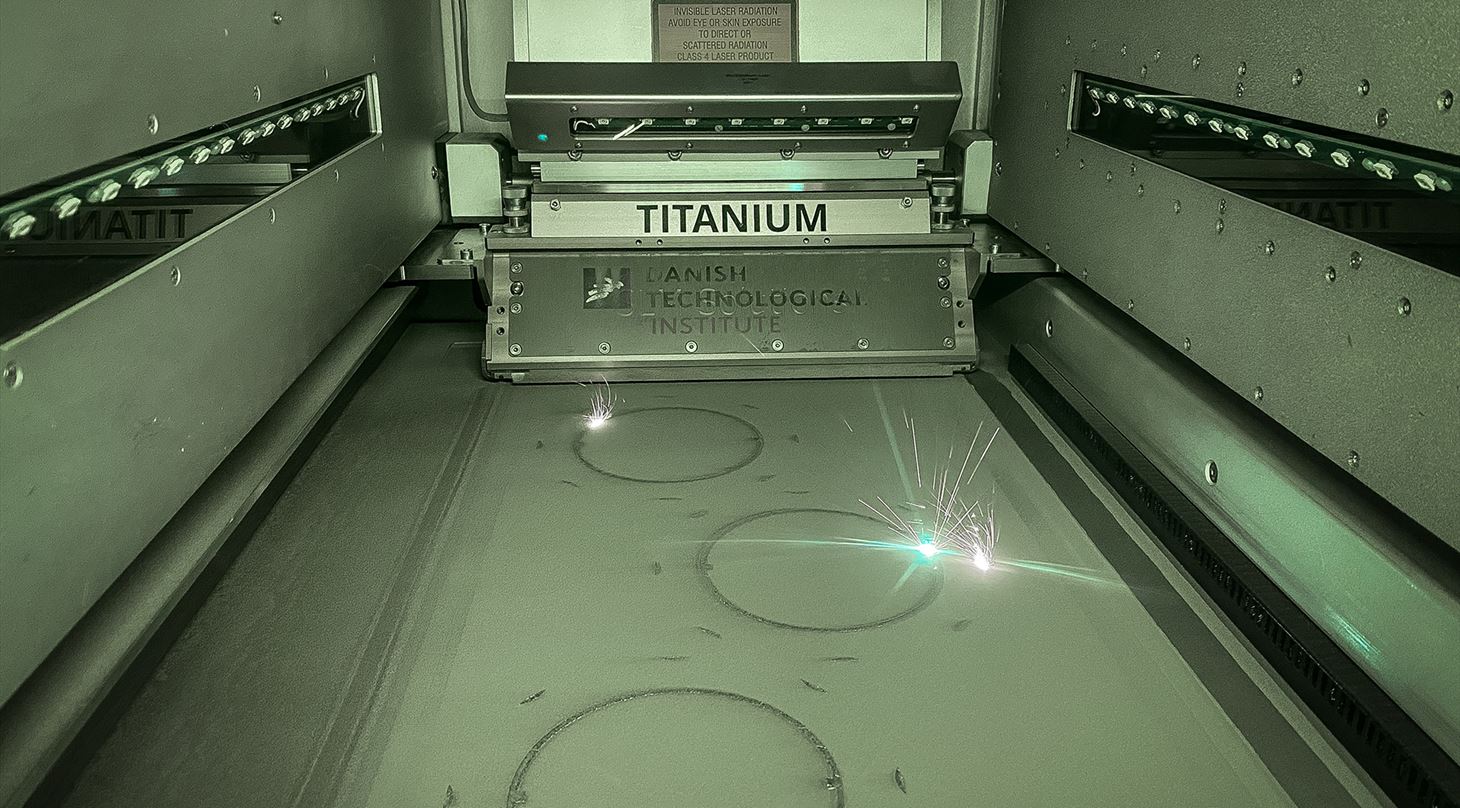
3D printing can reduce supply chain vulnerability
More flexible production with additive manufacturing methods can reduce the vulnerability of Danish companies in supply crises such as during the COVID-19 decommissioning.
COVID-19 has shown how traditional supply chains can come under pressure when borders suddenly close and suppliers are forced to stop production. Additive manufacturing methods, such as 3D printing, can help protect the industry against the effects of similar crises in the future. This is pointed out by the Danish Technological Institute, where focus is on developing and optimizing additive manufacturing methods for Danish companies.
- During the first COVID-19 wave, several manufacturing companies have had problems keeping production running - among other things because they could not obtain components from subcontractors due to closed borders. The more specialized the items, the less likely it is that you will be able to buy the components locally. Another challenge has been that manufacturers around the world have simply had to shut due to the risk of infection because there were too many people in production, says Jeppe Byskov, 3D printing expert and director at the Danish Technological Institute.
Let us help you with 3D printing production
He points out that a number of these problems could have been avoided if more companies had considered additive manufacturing methods. Here, the digital file is the production basis, and with 3D printing, the items are produced directly in the printer, so fewer people are required on the factory floor for the production itself. It offers a number of benefits - especially when the traditional supply chains are under pressure
- The first thing that stands out is that it is easier to send a file than an item. The item must cross borders while it is extremely fast to send the file to have it produced locally. That is an advantage if there are closed borders, or if you experience problems with customs barriers, says Jeppe Byskov.
With 3D printing, the item is built from scratch, and it is possible to integrate a large number of sub-components and functions. So there is no need for subassemblies or assembly at the end, which reduces the number of process steps, and you avoid logistical challenges with components that need to be sent back and forth.
Fast development and production
- With additive manufacturing, is also significantly faster to restructure your production. When a 3D printer is lined up, it does not matter which digital drawing it has to produce - and production can be started very quickly. Some companies have already taken advantage of this during the global pandemic, says Jeppe Byskov.
This includes the Danish company ExamVision, who saw an opportunity when dentists and surgeons in Denmark resumed work after the shutdown in March - now with a requirement for a face visor to reduce the risk of infection. In less than three weeks, ExamVision developed and produced 4,000 visor adapters so that the visors could be mounted directly on the company's loupes. These visor adapters were produced with 3D printing at the Danish Technological Institute
- The entire order was delivered within a week, and in total the process took no more than three weeks including three design iterations, testing and finished production. In fact, the shipments took the longest time, as the files could be delivered immediately, says Mads Østergaard, Team Manager at the Danish Technological Institute.
Minimum inventory
In addition to the fast delivery time, there is no need to maintain a large inventory for additive manufacturing. Instead, the items can be printed on-demand when needed.
As a bonus, you get an additional advantage if you have components that have to be handled automatically by robots. With the digital drawing, you already have the exact geometry of the item, and therefore it is easy to design and produce a gripper that fits - and it is fast to modify if corrections have to be made along the way. The same applies to assembly tools and fixtures.
On the other hand, you need to be aware that the material selection for 3D printing is a little more limited than for traditional production, although new possibilities are constantly emerging. In addition, you get a different surface quality from the 3D printer than what you know from e.g. a milling process. As with all other manufacturing methods, it is therefore essential to specify the requirement for surface quality, as it helps determine the finishing that the items must undergo in order to achieve the desired final quality.
A future with simulations and virtual factories
As the additive manufacturing technologies gain ground, there are also some exciting synergies - for instance between 3D printing and digital simulations. With the digital file, you can simulate your entire production before pressing 'print'. This increases the probability that the finished product will be as desired. It also means that the prototype process becomes much more compact and efficient.
- At the same time, it will be much faster to establish a production setup if you can just assemble a digital network of 3D printers that are not necessarily located in the same place - e.g. one for nylon and one for metal.This way, the ‘factory’ becomes more virtual and it can be located in several markets. If the 3D printers are identical and the print specifications and parameters have been locked, you can achieve identical results without being dependent on the local operator's qualifications, Jeppe Byskov concludes.
The Danish Technological Institute is constantly working to develop and optimize additive manufacturing - and not least 3D printing - so that Danish companies can benefit even more from it.