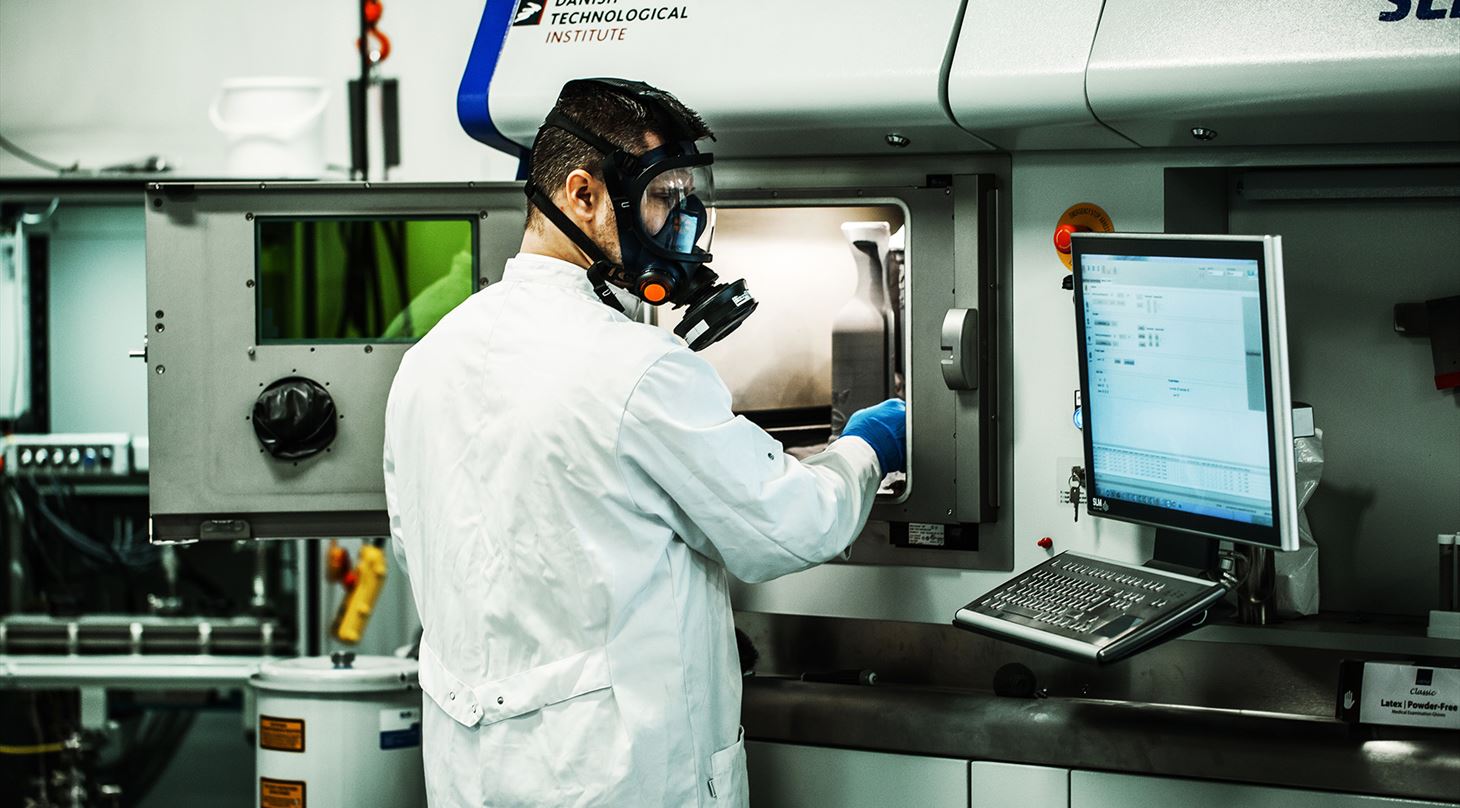
Additive Manufacturing in metal is safe for production
There are no health and safety issues with 3D metal printers, as the printing process itself does not cause harmful health effects. This is evidenced by recent studies that the Danish consultancy Niras has carried out in the Center for Industrial 3D printing at the Danish Technological Institute. The studies were carried out as part of the AM-LINE 4.0 project, which focuses on the industrial rollout of 3D printing in metal. However, there are some things to be aware of during preparation and post processing.
Isn't it dangerous to work with industrial scale additive manufacturing? The question is becoming more and more common as the technology advances, and more and more companies are becoming interested in the working environment aspects of additive manufacturing.
During recent years, additive manufacturing has moved from prototype tools to industrial manufacturing, and as part of this movement the printers have undergone a tremendous development where both print capacity and print speed has gone up, making real line production possible. Now, the technology is even more relevant for companies in the process industry - especially those working with special production, special items, small series, and high levels of development and prototype manufacturing.
However, this development has also led to uncertainty - among other things concerning work safety and the working environment - and for some companies this is a barrier. At the Danish Technological Institute, Niras has reviewed the Center for Industrial 3D Printing, and we would like to share knowledge and experiences from the studies and thus shatter some of the myths that additive manufacturing in metal should be dangerous.
An additive manufacturing technology
Before looking at the working environment, it's worth attaching just a few words to additive manufacturing as a manufacturing process, so we know what we are dealing with. The common denominator of the various additive manufacturing technologies is that they create a three-dimensional object layer by layer – that is why it is an additive manufacturing technology as opposed to e.g. machining which removes material from a raw subject.
Contrary to a traditional manufacturing process where one must 'be able to access the item from the outside', the additive manufacturing process does not have the same limitations, and thus it is possible to construct very complex items that could not be made otherwise. Furthermore, there are no auxiliaries involved, so the manufacturing process is less resource-consuming and fundamentally environmentally friendly.
In the AM-LINE 4.0 project, Niras has only looked at the working environment in terms of additive manufacturing in metal, where the whole process takes place in a closed chamber. Here, the item is printed on a metal plate by melting metal powder on the plate with the help of lasers - a bit like welding, just lightning fast, robot controlled, and one layer at a time. That way, the item is built layer by layer, and after each layer new powder is applied over the item in an ultra-fine layer, and the platform is lowered correspondingly to construct the item in a 3D shape. Finally, all the powder that is not fused is removed, and the 3D printed item remains.
Completely clean production process
Some might think that 3D metal printers are a kind of '3D copier' – similar to the smaller FDM printers. But in fact, the entire printing process is closed in, and the printing chamber is protected by inert atmosphere, just as when welding, so there is absolutely no risk of spills of metal fumes, dust or gases while printing. The measurements from Niras thus show that the process is perfectly clean.
No welding fumes are formed because of the protective gas - nitrogen – which protects the printing process from any oxidation. Nor is UV light a problem, as the chamber glass, like welding glass, protects it from light which is harmful to the eyes (although you can see through it) and thus there are no risks in the printing process itself in relation to physical and chemical influences.
Noise is also absent during the printing process due to the efficient encapsulation, but the traditional post processing can be noisy - however, Niras did not experience any problematic or annoying noise during the review of the Center for Industrial 3D Printing.
Regarding post processing, this will often be required to achieve perfectly fine and smooth items. However, the post processing consists of conventional grinding and polishing processes, which are well known and can be handled without any special risk.
Powder dust may occur
When the printing process is complete, you need to remove the item and clean it of metal powder, and here dust may appear in the air when you open the chamber.
At the end of the printing process, the item is 'buried' in powder, so the platform is ascended, and all the powder is sucked up and filtered for reuse in the machine. This process may be more or less automated depending on the printer model, and with the more manual models, there may be a risk of powder escaping. Cabin solutions, integrated vacuum cleaners and the likes can solve this task, and during the more manual processes, gloves and respirators are used to prevent the powder dust from being inhaled. The powder will then settle and not be swirled again.
The print chamber itself is quite easy to vacuum, whereas the items are cumbersome and must be completely cleaned of dust. During this process, gloves and respirators are worn.
Avoid heavy lifting
Powder for recycling must be filtered to remove melt drops and 'slag' as they will otherwise interfere with the process. The filling of new powder and powder for recycling is automated to varying degrees, but on smaller machines it is typically done with metal bottles, which are fitted with flanges and which must be mounted precisely. These metal bottles are heavy, so it is advised to have a crane or other lifting device to avoid ergonomic problems with heavy lifting in inappropriate working positions. Other than this consideration, there are no other ergonomic issues associated with the additive manufacturing process.
The technology is ready for industrial use
Additive manufacturing in metal is neither harmful nor problematic to the working environment, and due to the effective containment, the risk is smaller than during traditional welding and machining processes, and generally there will be no health or chemical hazards.
However, you need to have a realistic idea of the long cycle times as well as the degree of post processing, and you need to put a lot of thought into setting up and integrating the 3D printers in the company's workflow, as the process is very different from casting processes and machining.
For the same reason, it is important to have a working environment review of the production - not only of the additive manufacturing function itself, but also of the associated functions. This ensures that all conditions are taken into consideration, including both physical conditions such as lighting, noise and space, but also ergonomic conditions such as working positions, lifting and technical aids as well as suction and ventilation.
Finally, just take some simple precautions such as making sure that the necessary technical aids are available, and that gas installation and alarms have been thought of. In addition, the employees must of course be instructed in the processes, as well as to use the necessary protective equipment and follow safety procedures like everywhere else.
If you take this into account, there’s no need to be afraid of diving into additive manufacturing in metal – the technology is completely ready for the factory floor.