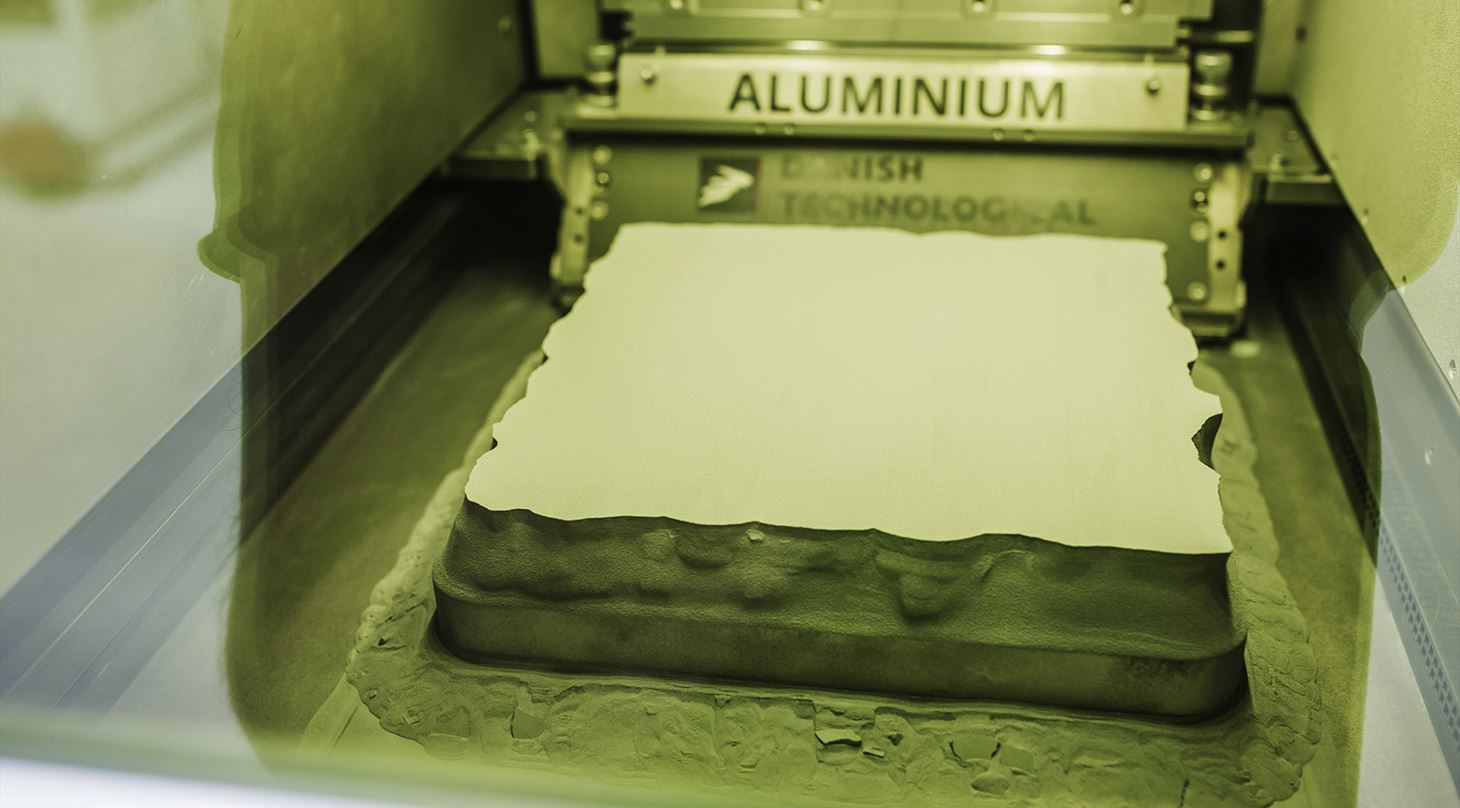
Powder Bed Fusion – a fast-moving technology
Powder Bed Fusion is one of the most widely used 3D printing technologies on the market today, and the technology has gained a strong position in the industry. This is not without reason, because Powder Bed Fusion offers several exciting opportunities and is a profitable solution in many respects. At the same time, the development of the technology is moving fast, and this allows for new solutions to potential challenges.
When you’re getting started with Powder Bed Fusion, the first step is to choose the material you want to print in - and with Powder Bed Fusion you can print in both metal, plastic, and ceramic. The choice of material also helps to determine whether the printing should be done with an electron beam or laser, which can be confusingly similar, as they are both powder sintering technologies. In powder sintering, a thin layer of powder is spread on a build platform, after which the powder is either melted together with a laser or electron beam - or glued together with a binder - and subsequently the next layer of powder is applied to the build platform. This process repeats until the part is printed.
Try an online course about Powder Bed Fusion
Two different machines - each with its own advantages and disadvantages
Although both electron beam and laser are powder sintering technologies, there are large differences in the structure of the machines, which also offers different advantages and disadvantages for the two types of print.
If you instead choose to glue the powder together with a binder, the glue must subsequently be burned away from the powder. This is followed by the sintering process, where the part is heated to near the melting point, and the powder is sintered together in the places that previously had binder. YOU CAN READ MORE ABOUT THIS PROCESS HERE
However, the most common printing technology is printing with a laser or with another heat source, such as an electron beam, where the powder is melted together. If you choose to print with a laser, the laser beam can move freely through the air, but in return it is necessary to use a support structure, which requires post processing to have a successful printing process.
- Support structure is very important with the laser technology when printing in metal, as the support structure keeps the part attached to the build platform. Otherwise, the part would risk bending up or deform due to the heat. But by fixing your parts with a support structure, you get around that problem, says 3D-printing specialist Lasse Haahr-Lillevang from the Danish Technological Institute.
- If you use an electron beam, it requires a vacuum inside the machine, which complicates the technology compared to if you use a laser. On the other hand, an advantage of electron beam machines is that there is typically a lot of heat in the whole area, and this means that you do not have to use as much energy to melt your powder, and thermal gradients are not as great a challenge, explains Lasse Haahr -Lillevang.
In the video below, you can hear a little more about Powder Bed Fusion
Increased industrial interest in complex geometries
Today, Powder Bed Fusion covers a wide range of sectors in the industry, where the major drivers of the technology are the dental, automotive, aviation and not least the aerospace industry, where virtually all rocket nozzles are 3D printed.
- In a Danish context, it is especially industries that make their own injection moulds as part of their production that adopt the technology, says Lasse Haahr-Lillevang and adds that the demand for Powder Bed Fusion in the food industry has increased.
Let us help you with AM production
- The reason for this is that you can make some really complex geometries, and you avoid a lot of assemblies compared to if you had to process and subsequently assemble the part. You can save money on this, and at the same time you can avoid bacterial growth in joints, says Lasse Haahr-Lillevang.
Development of green lasers for printing with copper
When it comes to the development within Powder Bed Fusion, according to Lasse Haahr-Lillevang, it is the printing of copper with laser and the development of post processing methods that you should keep a watchful eye on.
Especially copper has been a challenge to print with laser, because copper has a high reflectivity, and therefore a large part of the energy will reflect back into the laser.
- Typically, you have an infrared laser when printing in steel, aluminium, titanium, etc. And if you increase the intensity, it can also be used for copper printing. But if you replace the infrared laser with a green laser, you take advantage of the fact that copper absorbs the light much better with green light than with infrared light. In this way, you can get the energy absorbed by the material more efficiently - and copper is a really exciting material to work with, because it has a high conductivity, says Lasse Haahr-Lillevang.
En route towards automated post processing
At present, there are several different methods to remove the support structure from the 3D print, but most often the support structure is sawed off or removed manually with pliers. Common to both methods, however, is that they require many working hours, and therefore it can be an advantage to automate the process.
- There is a lot of focus on automating all or part of the post processing. This includes removal of the support structure, where automation will lead to savings and higher efficiency, says Lasse Haahr-Lillevang.
Current challenges also hold great potential
Developments in Powder Bed Fusion also face a challenge: the post processing of the inner geometries, which are difficult to polish.
- Because it is powder that is melted together, the surface will be rough. Therefore, the part will often be post processed to allow for better and easier cleaning. But if you are dealing with a part with an inner geometry, it can be difficult to get in and polish, says Lasse Haahr-Lillevang.
The work therefore consists of making it possible to process the inner geometries on the 3D-printed parts. This will be a great advantage in relation to cleaning and air resistance, and in addition it will be a cheaper solution than if you had to use welding instead.
- 3D printing has an advantage because you have a great deal of design freedom. Therefore, we currently have some projects, where we’re investigating how the internal polishing can be done - and not least how it can be made most profitable. So, there is great potential in the challenge, which will benefit many Danish companies, says Lasse Haahr-Lillevang.
The Danish Technological Institute can help you get started with 3D printing
If your company is interested in embarking on the 3D printing journey, there are several approaches depending on which business case is of interest.
- If, for instance, it is a large company that has a lot of products, then the Danish Technological Institute can help make a screening of the products to define where it would make sense to start with 3D printing in relation to existing challenges, says Lasse Haahr-Lillevang, and elaborates:
- The Danish Technological Institute can help companies in many ways, either by validating geometries for printing, helping with guidance and design optimization for the technology as well as delivering printed and finished components for both single and series production.
Read about the other AM technologies
Furthermore, the Danish Technological Institute offers courses – online and physical - where companies can learn more about the good business cases for 3D printing as well as the various design possibilities.