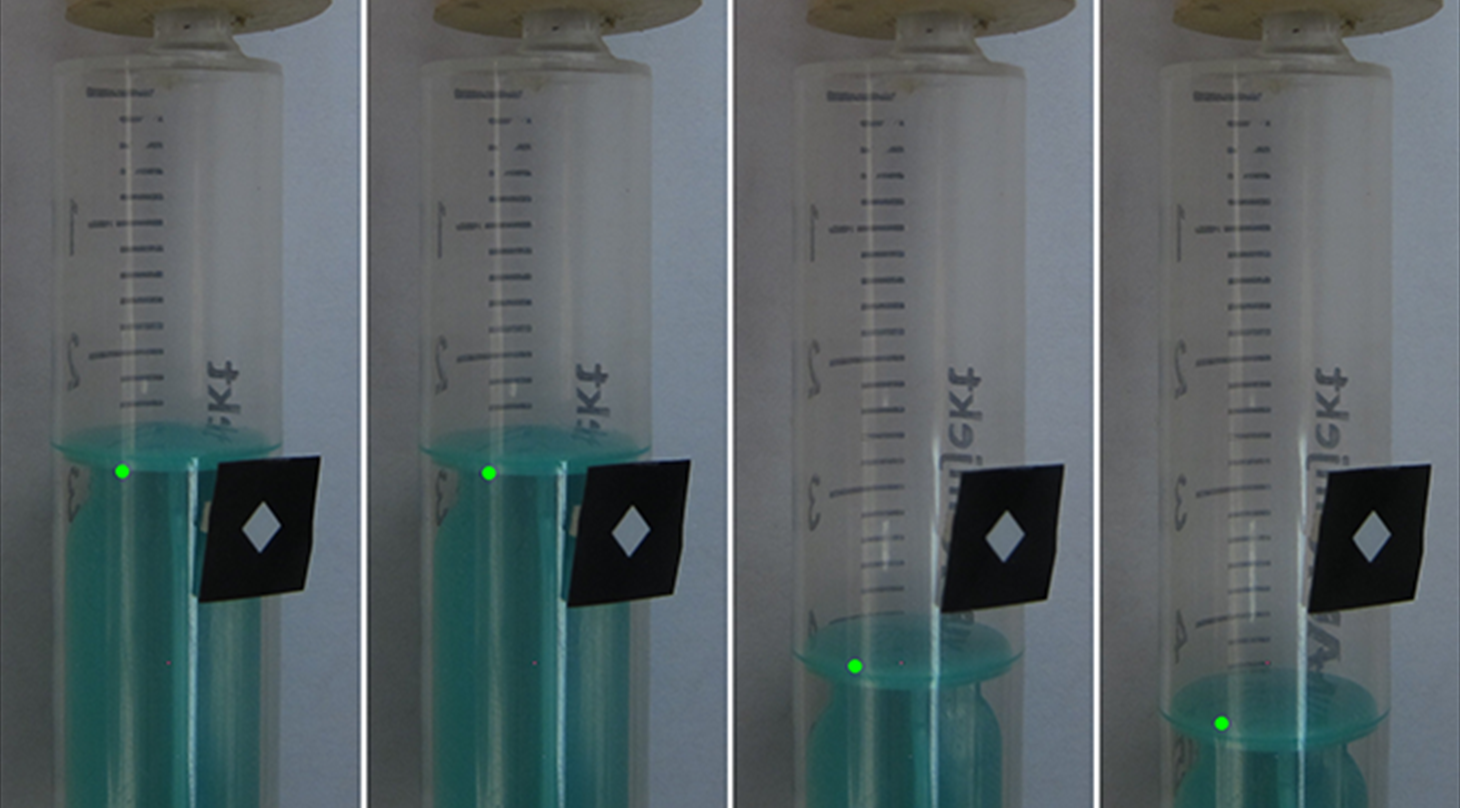
Plunger stopper movement during air transport at low pressure
We all know the feeling of pressure in our ears when we are on a plane that is taking off. This is because the air pressure decreases as you ascend higher into the atmosphere. But how do packaging and products behave during air transport? - Does plunger-stopper displacement under low atmospheric pressure risk impacting sterility and container closure integrity (CCI) in prefilled syringes?
Larger cargo planes typically have a pressure shell, which ensures that the pressure in the cargo hold is 0.75 bar when the plane reaches 10 km altitude. However, the pressure in smaller planes without a pressure shell can drop as low as 0.55 bar (55 kPa). This means that the pressure is almost halved, and this can lead to mechanical changes in packaging and products. For example, the packaging may burst, or there may be unwanted movement of critical parts. If a product is transported by truck through a mountain pass at an altitude of 3000 meters, the pressure is 0.7 bar, so even on land, the pressure can be significantly lower than at sea level.
One of the more recognized standards for testing air transport is International Safe Transit Association standard 3A (ISTA 3A) for air and truck transport. ISTA 3A, 3B and 3E are present on FDA’s CDRH Recognized Consensus Standards Database.
The ISTA 3A conditions are at a pressure corresponding to height of 14,000 ft or 4,267 meters. The pressure at a given height is set according to table X1.1 in the ASTM D6653 standard. The test object is taken to that pressure at a rate equivalent to 1,000 ft every 30 to 60 seconds and finally up to normal atmospheric pressure with the same rate. The test follows and improves on the procedure in: “Risk Mitigation of Plunger-Stopper Displacement Under Low Atmospheric Pressure” [1]
One of the situations where change during air transport is important is for prefilled syringes or prefilled cartridges where it is a concern if the plunger moves to a non-sterile area collect microbes that are transferred to the contents of the syringe or cartridge, in other words impacting sterility and container closure integrity (CCI). We have illustrated how plunger movement can be measured below.
Case Study: Prefilled Syringes and Cartridges
At the Danish Technological Institute, we have created a setup capable of generating a controlled vacuum to simulate the low pressure experienced during air transport while simultaneously capturing images of one or more items. The image at the top of the article shows an example of such a measurement, where a disposable syringe is sealed with a stopper, and then the pressure is reduced while the movement of the plunger is recorded. In the first two images, there is no change in the position of the plunger, even though the first image was taken at 1 bar and the second at 0.67 bar. The last two images were both taken at 0.28 bar, with a 20-minute interval. The plunger moved between the first and last images, and it continued to move even though the pressure remains the same.
To gain a better understanding of this behavior, we created a series of images where we used a computer to measure the position of the plunger over time. The results are shown in the figure below. The pressure ramp used here simulates an ascent of 400 meters per minute. (follows ISTA 3A). There is no linear relationship between pressure and plunger position, but it is clear that after approximately 1000 seconds, the plunger begins to move, and once it moves, it does not stop until about 3000 seconds into the experiment, even though the pressure remains unchanged. On the ramp back to 1 bar, the same phenomenon is observed, where the plunger only begins to move after some time.
Objects at rest typically have a greater resistance to movement due to surface roughness than objects that are already moving. What we observe here is that the pressure difference on the plunger must overcome the static friction. Once it starts moving, the plunger moves easily because the dynamic friction coefficient is lower than the static one. This type of behavior can be difficult to predict or simulate because it depends on the material and possible lubrication.
Our Capabilities
At the Danish Technological Institute, we have developed a setup that can measure how products and their packaging behave when the pressure is reduced. The tests can be done at temperature-controlled conditions at 23 °C or at other temperatures. In addition to image analysis, the measurements can be combined with a vibration test for an even better simulation of air transport. Companies can use these results to confirm that their products can withstand air transport, both for their own assurance and for product approval by authorities. Our department does most ISTA tests.
Measuring plunger movement during temperature cycling is also possible.
Contact us for more information at phone 72 20 16 24 or 72 20 24 85, email: sbv@teknologisk.dk or jae@teknologisk.dk.
Se video