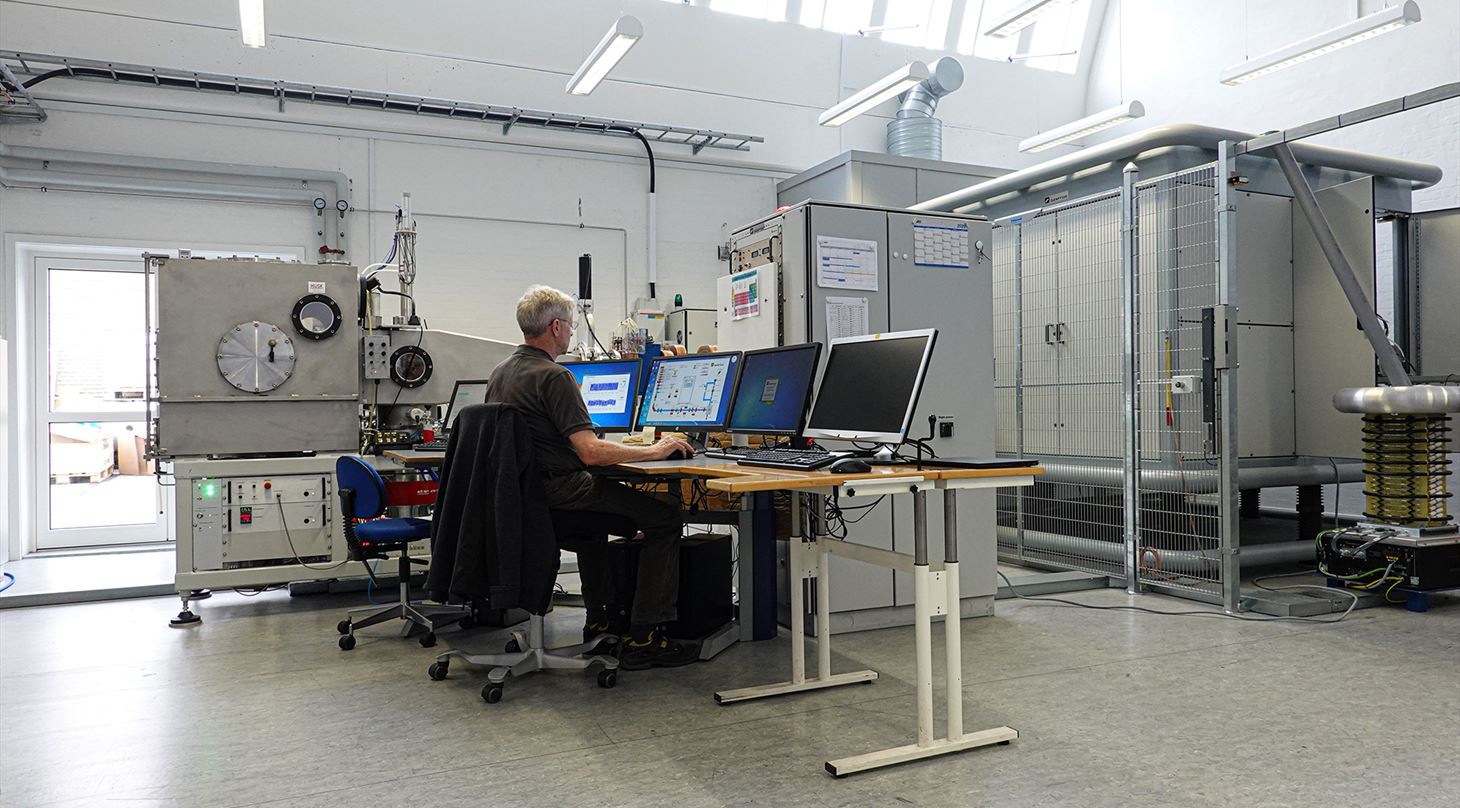
Ion implantation solves many production problems
Ion implantation covers a group of surface treatments, which have their origin in advanced particle physics. However, at the Tribology Centre at Danish Technological Institute, the technology has been further developed and perfected for several specific, industrial applications.
The Tribology Centre runs two advanced ion accelerators, which are primarily used for industrial surface treatment of production tools, but also for research and development. The development work is especially aimed at finding new methods to change the physical and chemical properties of material surfaces. The Tribology Centre has many years’ experience with ion implantation of a wide variety of elements for various industrial applications.
By ion implantation, ions (electrically charged particles) are accelerated up to high velocities over an electric field of up to 200,000 V. The ions are shot into a surface of e.g. a production tool, generating special properties in the surface region. The process temperature is always below 150 ˚C, which makes it suitable for many types of materials.
Standard coatings and ion implantation
The Tribology Centre's portfolio of surface treatments for production tools include the following:
IBAD-DLC
IBAD-DLC means Ion Beam Assisted Deposition of Diamond Like Carbon and it is a unique, self-lubricating low-friction coating, providing reduced friction when forming e.g. tin cans for foods and industrial products. Besides this, the IBAD-DLC coating is also used for protection of the lacquer, polymer or tin coating applied to the sheet metal to prevent corrosion and direct contact between the packaging material and the product.
Figure 1: IBAD-DLC coated tool for cutting of a metal lid for food packaging. Prior to IBAD-DLC treatment, this tool has been coated with titanium nitride (TiN). The tool is mounted inside a vacuum chamber.
Figure 2: Tool for forming of ring pulls on cans.
CrN-SS – SuperSlip
CrN-SS combines a PVD coating (CrN-SD) with subsequent ion implantation, where ions are shot into the outer surface layer. The ion bombardment changes the condition and chemistry of the surface and gives significantly improved release properties in plastic injection moulding, while also extending the life of the mould parts.
Figure 4: Plastics tool with improved release properties after ion implantation.
Cr-Plus
Cr-Plus is ion implantation with chromium ions used for corrosion protection of air vents on injection moulding tools. When shooting chromium into the outermost surface of the steel, the surface is alloyed in the surface region to an extremely high corrosion resistance with up to 35 % Cr concentration in the outermost surface.
N-Plus
N-Plus covers ion implantation with nitrogen, which provides wear resistance to precision tools and to extremely sharp cutting edges, where even a thin hard PVD coating will round off the knife edge to a degree where the knife will become too dull.
Advantages of ion implantation
- Reduced friction, especially by forming of metal packaging
- Reduced corrosion around air vents in injection moulding
- No geometric changes
- The original surface finish is maintained
- Low process temperature. The temperature can be controlled depending on the material
- The process can be performed locally and on already finished parts
- Can be applied to metals, polymers, and elastomers
- Possible to implant with various elements
- No risk of peeling-off, as ion implantation is not a coating, but a treatment which is mixed into the surface
- Extremely good adhesion of IBAD-DLC because the coating is partly mixed into the surface
Application examples
The plastics industry: Improved release in injection moulding and elimination of corrosion in air vents.
The medical industry: Wear protection of medical products, e.g. increased lifespan of artificial cartilage, knee- and shoulder implants.
The packaging industry: Tools for cutting and forming of e.g. tin packaging. Protects against adhesion, wear, and damage to the protective film of the metal sheet.
Ion implantation of polymers: Increased hardness of several polymers, e.g. silicones, polyethylenes, etc.
Ion implantation of metals: Increased hardness of titanium alloys, aluminium alloys, various steel types, noble metals as e.g. gold.
Process details
By ion implantation a beam of high-energy ions (50-200 keV) is shot into the surface of a given material. The ions are hereby implanted into the surface and depending on the ion type and base material, they form new chemical structures and phases. The result is changed physical and chemical properties of the treated surface, which leads to increased hardness, altered release properties and/or improved corrosion resistance. Ion implantation has the advantage that it is possible to implant substances which cannot normally diffuse into or even be insoluble in the base material. Since ion implantation is not a coating, but a change in the structure and chemistry of the base material to a depth of less than one micrometre, there is no risk of peeling-off.
Top photo: The new ion accelerator at the Tribology Centre.