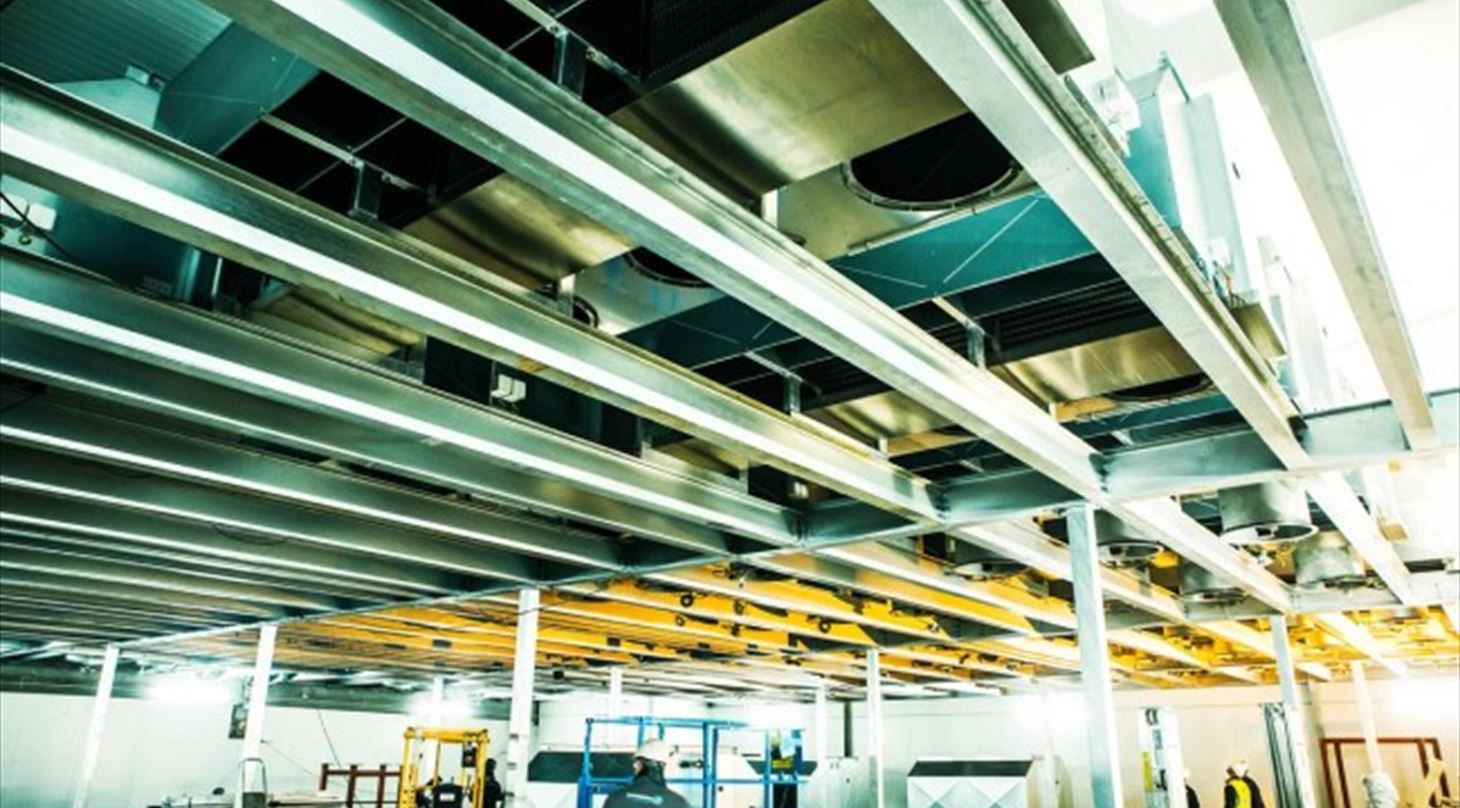
Chilling process design for an existing slaughter facility
Case story: Esfosa Spain
“DMRI assisted us in ensuring that production could continue undisturbed throughout the project. Detailed specifications for the chilling process, influencing meat quality and chill loss levels positively, was essential for the success of this complicated project. DMRI also provided support on demand throughout the construction period. We are pleased to have achieved a chill loss of 0,8 to 0,9%, and a process time of 14 hours on carcases of 86 kg.” says Chief executive Officer Fransisco Sorolla, Esfosa Spain.
Project data
Chilling footprint: 2630 m2
Slaughter cap.: 800 pigs/h
Duration: 2015-2019
Construction manager: Colomer Rifa
DMRI scope included
Chilling process specifications. Complete documentation of Quick Chill Tunnel, equalizing equipment and performance specifications such as air temperatures, process time, air flow, carcass spacing and all parameters relevant to ensure low chill loss and high meat quality in the final chilled carcasses. The specifications covered both the quick chilling area and adjacent equalizing rooms.
Building specifications for chilling areas. Extensive guidelines for correct construction of the insulated structure containing the quick chiller that ensures structural longevity even with frequent defrosting and refreezing in connection with cleaning. The specifications also defined best practice for interfacing with other building parts, pipe penetrations, vapour barrier integrity, insulated panel finish and steel column support on insulated floor.
Review of refrigeration contractor documentation. Thorough examination of the intended supply of the selected refrigeration contractor ensuring the quality of the delivered equipment along with satisfactory performance.
Supervision during installation and commissioning. On demand support through site visits and remote decision support.