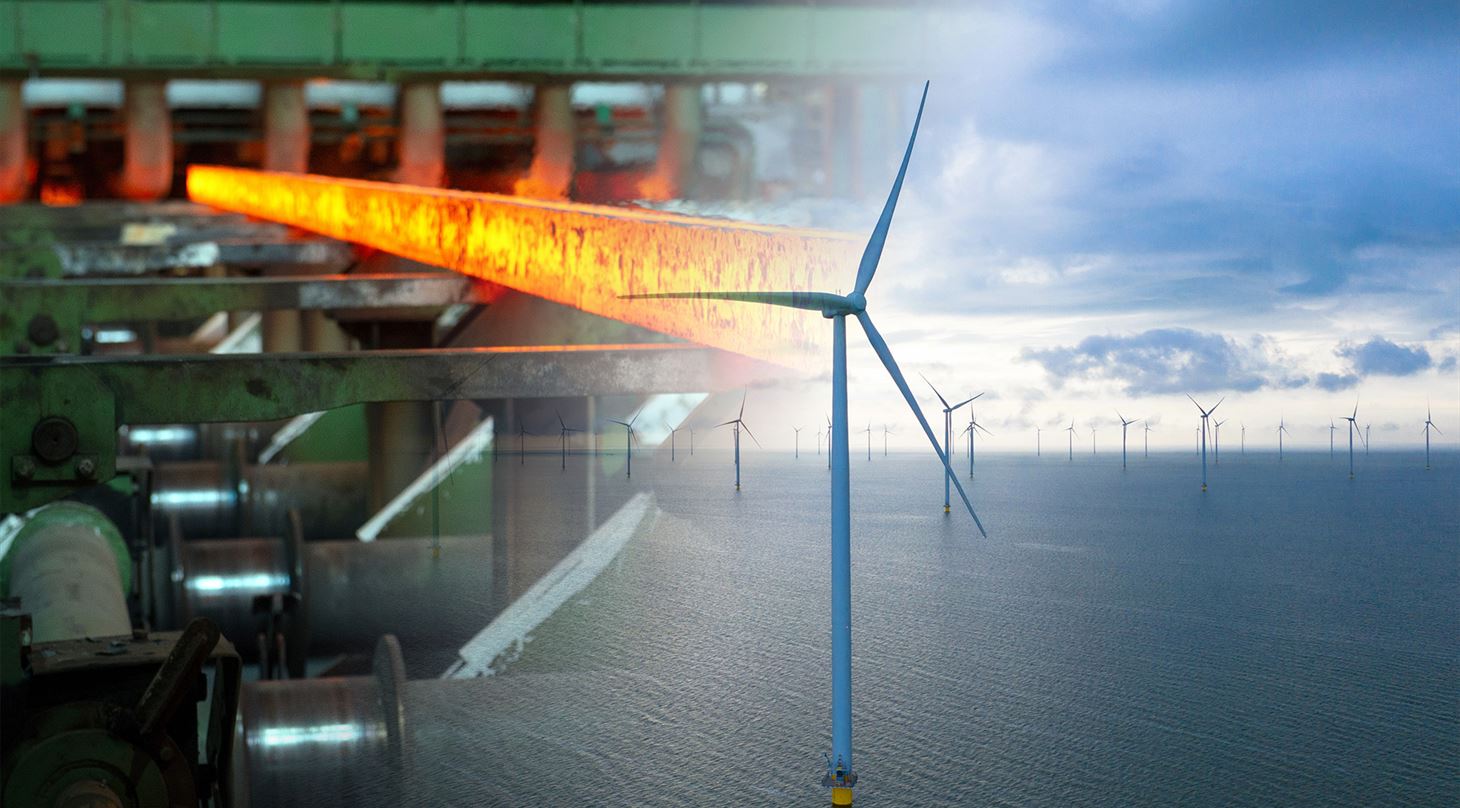
ZEROSTEEL: CO2-neutral steel production with innovative processes
9% of the world’s total CO2 emissions come from steel production. Since steel will remain an essential raw material in the future—particularly in the expansion of green energy solutions like wind turbines—it is vital to transition steel production to become CO2-neutral.
There are already methods to achieve this today, but they are very expensive and require a very high consumption of hydrogen, which in turn necessitates the expansion of a massive hydrogen production infrastructure.
The Horizon Europe project, ZEROSTEEL, aims to address this by developing cheaper and less resource-intensive methods for steel production. The project adopts a broad approach across the entire supply chain, exploring both optimization of well-established methods and the development of new, innovative techniques. The project integrates biomass gasification, green hydrogen from local networks, and electrolysis plants. Four new, more sustainable iron ore reduction processes will be utilized, including:
- Fluidized bed hydrogen-based direct reduction: Utilizes hydrogen from various sources to reduce iron ore.
- Rotary kiln direct reduction: Develops hydrogen reduction in rotary kilns, with the possibility of using biomass-based hydrogen.
- Microwave-assisted reduction: An electrified process that uses microwaves to heat and reduce iron ore.
- Hydrogen plasma reduction: Integrates hydrogen plasma technologies into the production of liquid iron.
These processes will be combined with advanced digital monitoring, detailed process characterization, and digital twins to optimize steel production and ensure high quality. Additionally, life cycle assessments will be applied to ensure environmental sustainability and economic feasibility.
The role of the Danish Technological Institute
A crucial part of optimizing these processes is understanding them in detail. This has traditionally been a challenge, as the processes occur under extreme conditions—for example, at temperatures of up to 1500°C or in controlled environments such as high-pressure flammable hydrogen gas—which are incompatible with traditional measurement equipment. However, the Danish Technological Institute (DTI) is capable of studying these processes using neutron and synchrotron X-ray analyses. DTI plays a key role in the project, leading a work package on advanced characterization.
In this work package, neutron and synchrotron characterization performed by DTI will be combined with optical emission spectroscopy (OES) and the development of a cognitive digital twin of the processes based on the measurements. This will provide the best possible tools to optimize the processes. Moreover, the iron ore and the produced steel will also be examined for imperfections and hydrogen content.
Overall, the project aims to develop methods that can reduce CO2 emissions from steel production by up to 90%. For more information, please contact Jonas Okkels Birk.
Facts About the project:
This project has received funding from the European Union’s Horizon Europe research and innovation programme under grant agreement No 101178435
Budget: EUR 5.0 million
Timeframe: October 1st 2024 – September 30th 2028
Website: zerosteel.eu
Social media: LinkedIn